Экскурсия на комбикормовый завод группы компании «Русагро» начинается с объяснения правил безопасности. Как и на многих предприятиях, здесь нельзя трогать руками работающую технику и перебегать перед машинами. Ещё нельзя отвлекать от работы сотрудников завода, без разрешения входить на объекты и самостоятельно что-либо включать.
Нам выдают на выбор каски белых и красных цветов, а также СИЗы и маски. Чтобы пройти на территорию завода, этого недостаточно, поэтому мы на контрольно-пропускном пункте ещё топчемся по специальному коврику, чтобы дезинфицировать обувь, и обрабатываем руки антисептиком. Только после этого нам можно идти на завод.
Пока мы идём к первой точке экскурсии, нам параллельно рассказывают про продукцию «Русагро», а точнее — про мясное направление. К слову, компания занимает третью строчку в рейтинге крупнейших производителей свинины в России. Производство представлено в трёх регионах: Белгородской и Тамбовской областях, а также в Приморском крае — в нём полномасштабно производить свинину начали совсем недавно.
В Белгородской области размещены 39 объектов, 34 из них — производственные площадки, где выращивают животных. Так, в год на площадках в Ивнянском и Волоконовском районах, а также в Шебекинском горокруге получают 650 тысяч свиней. В Ивнянском районе есть мясоперерабатывающее производство, на котором за год на убой отправляют 350 тысяч голов и ещё 270 тысяч — на обвалку.
Кстати, в Белгородской области не производят полуфабрикаты, но изготавливают полутуши, субпродукты и крупный кусок.
В число 39 производственных площадок Белгородской области входят также два комбикормовых производства, одно из них находится в Шебекинском горокруге, а второе — в Ивнянском районе. На последнем нам удалось побывать.
С чего начинается производство комбикорма?
Работа любого комбикормового производства начинается с пробоотборника. Сейчас его полностью реконструируют. Он нужен, чтобы «обезличенно» анализировать пробы: лаборанты не будут знать, с какой машины к ним на анализ поступила проба. Это современная система производства, стоящая десятки миллионов рублей. Проект планируют закончить и сдать в октябре, а потом начать полностью им пользоваться.
Пока идёт реконструкция пробоотборника, лаборанты вручную берут пробы с транспорта, на котором поступает сырьё, и производят его входной анализ. Анализы берут в основном экспресс-методом. Благодаря ему можно определить, есть ли вредители, какова влажность груза и другие основные показатели.
Сырьё в основном привозят поставщики, которых выбрали на торгах. Среди них могут быть как крупные фирмы, так и мелкие фермеры. После проведения входного анализа, если все нормы соблюдены, лаборант создаёт анализную карту, с помощью которой автомобиль может проехать на территорию завода.
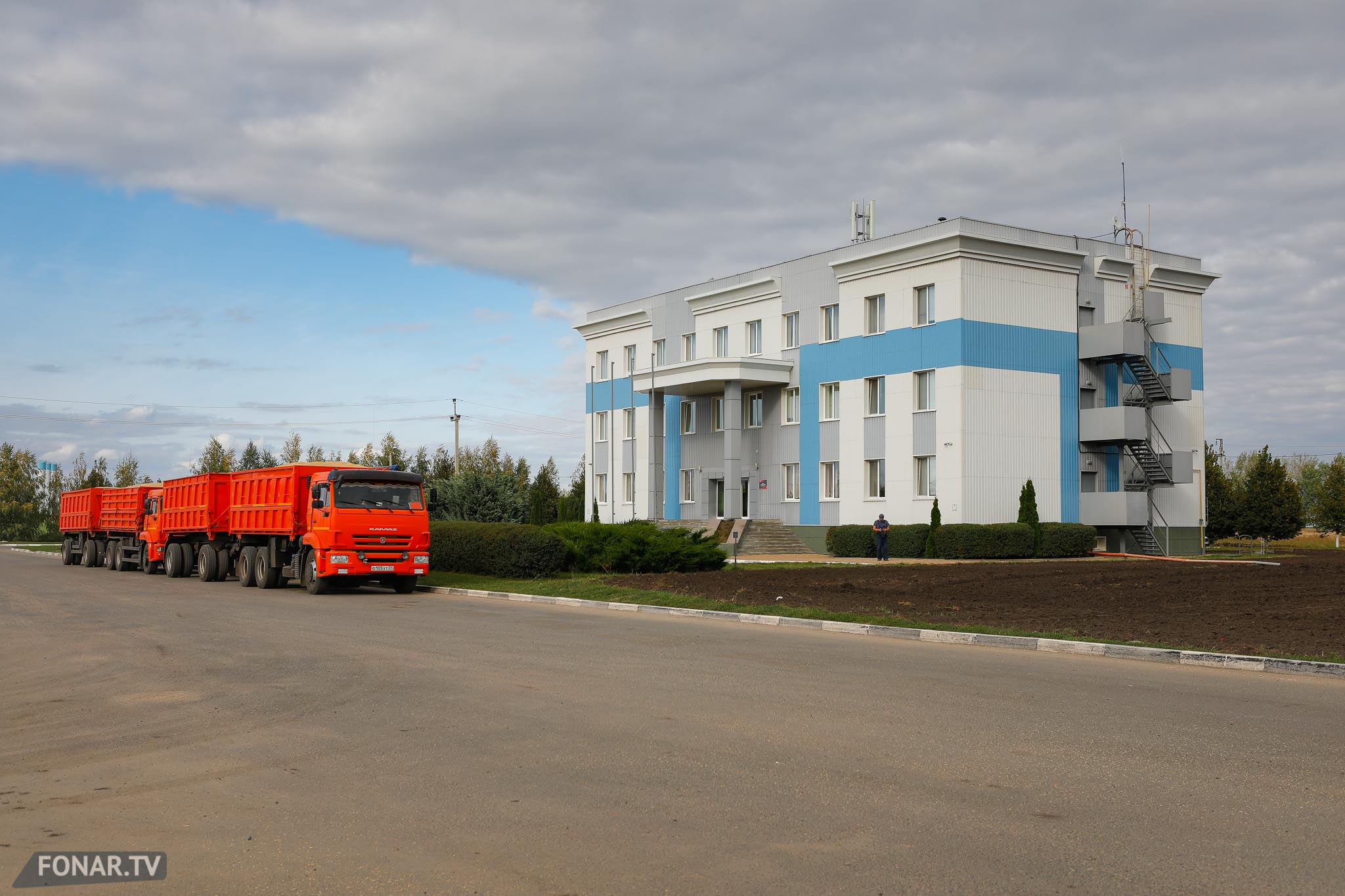
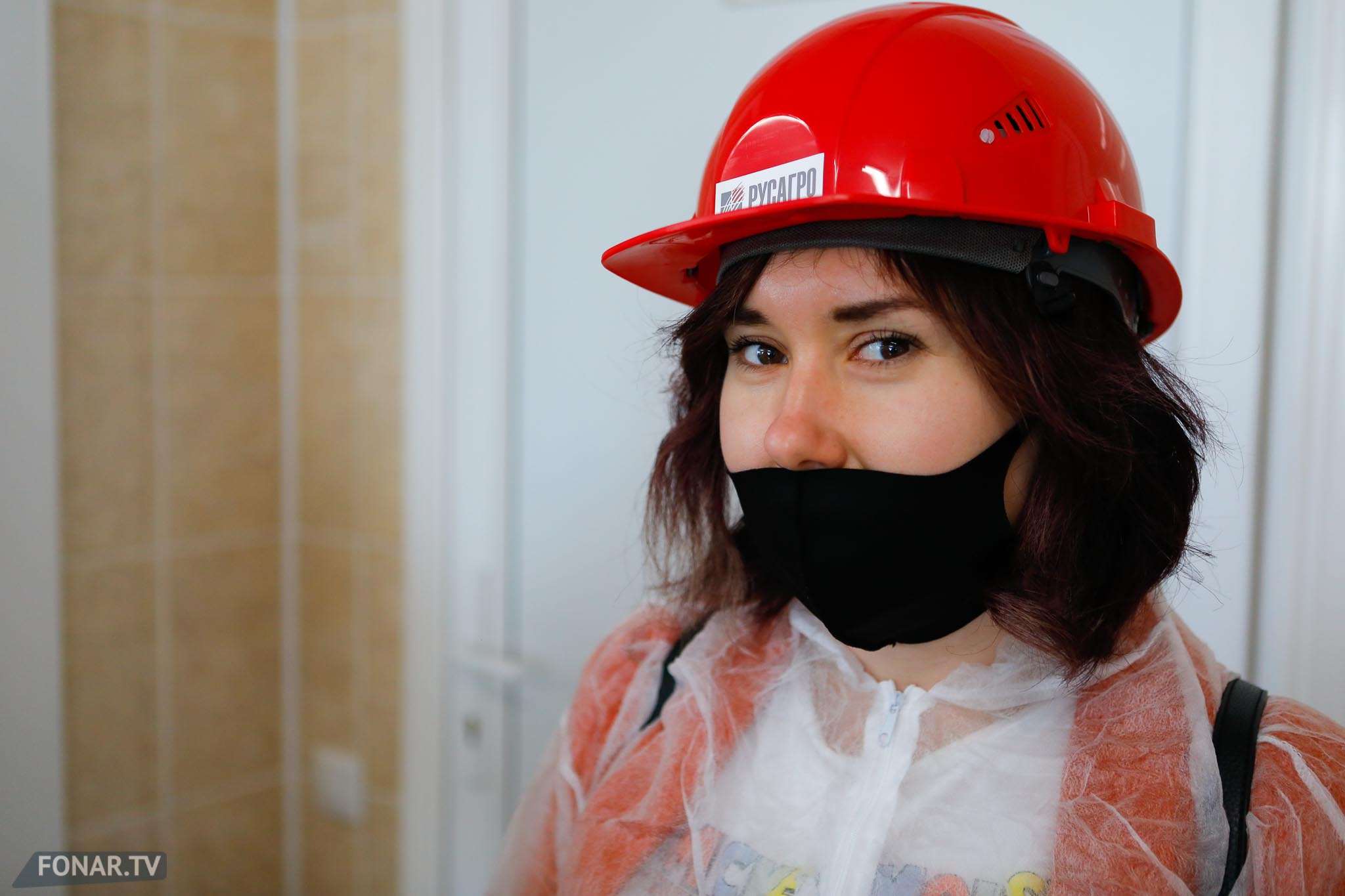
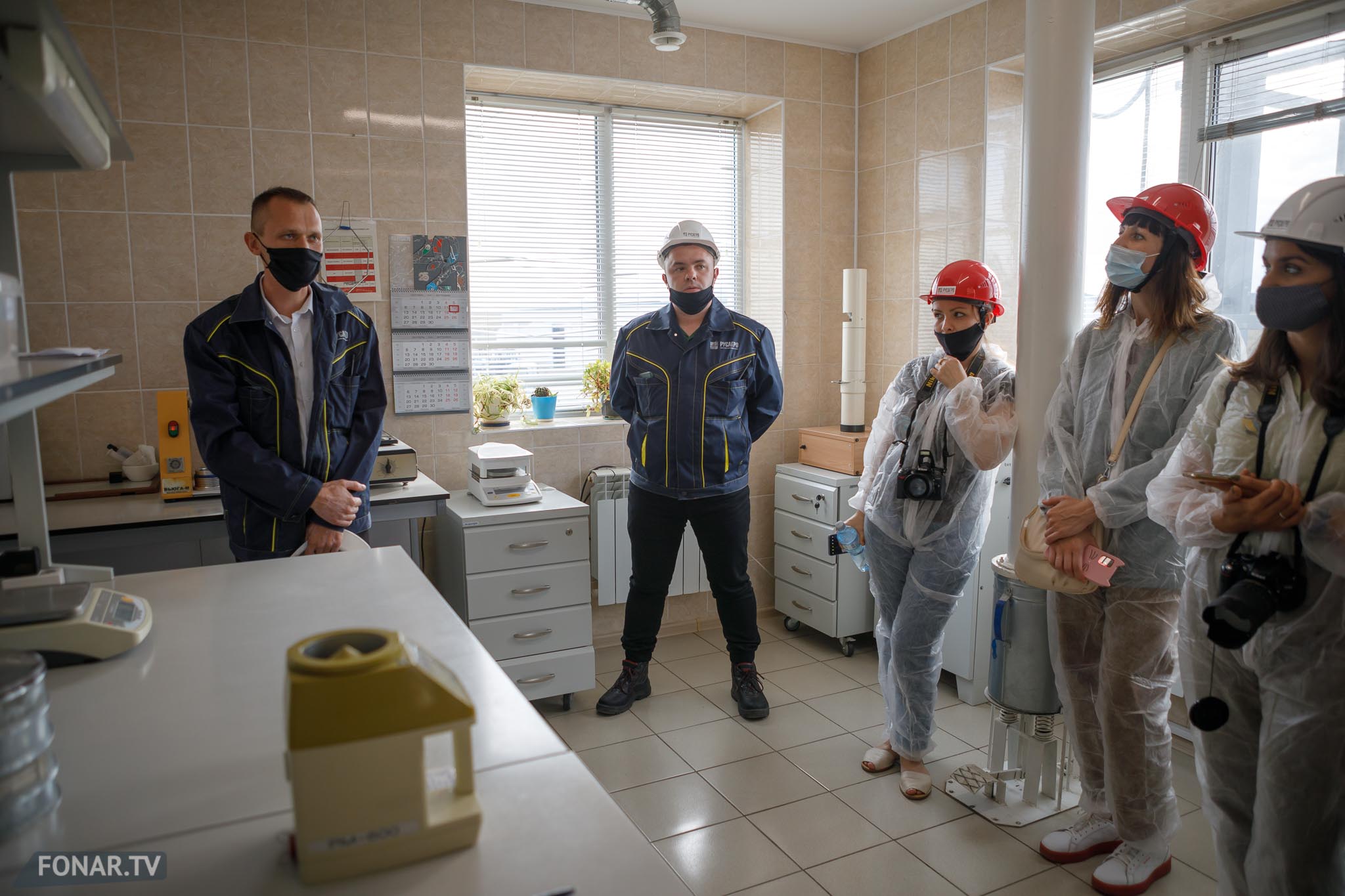
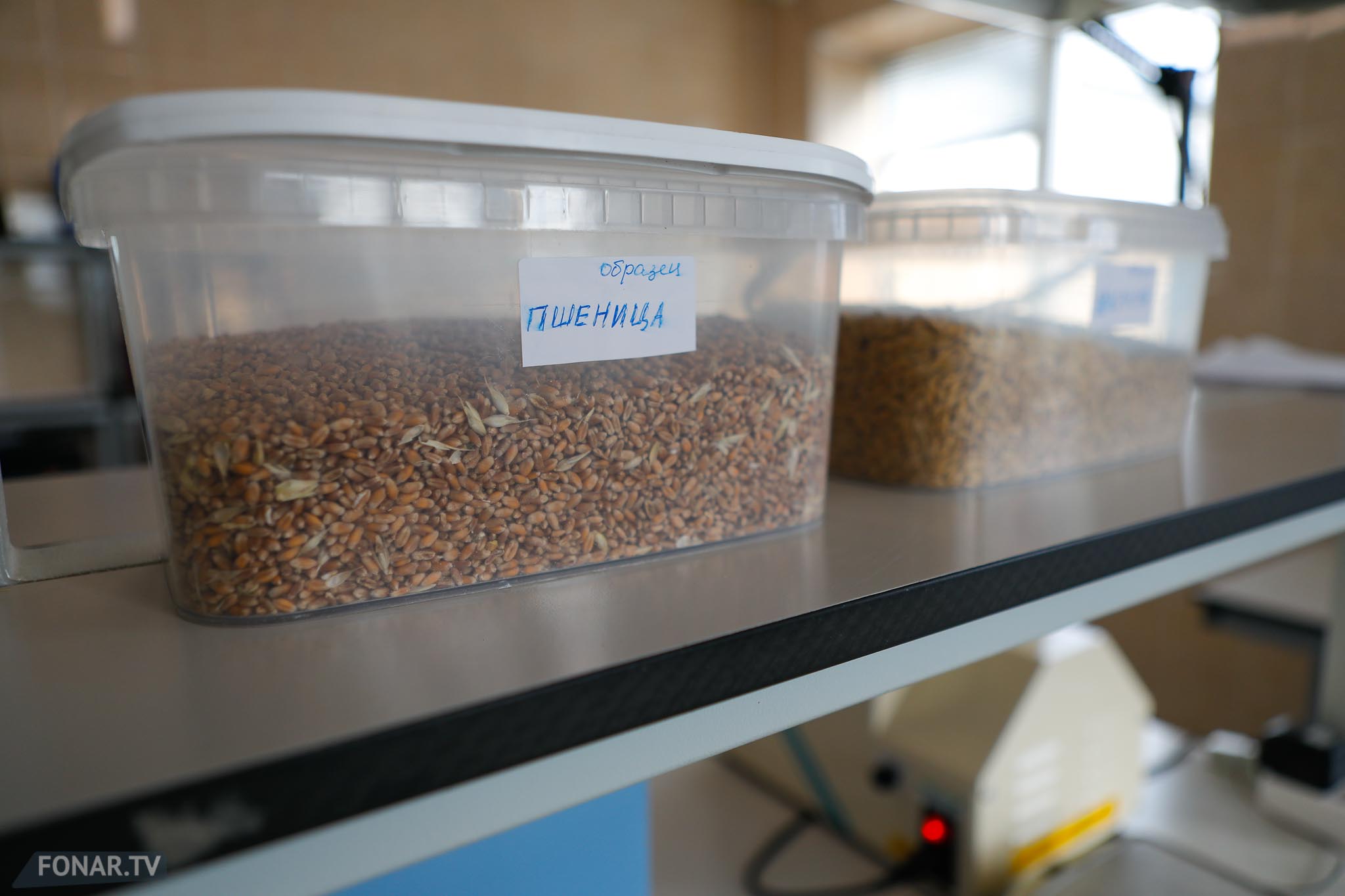
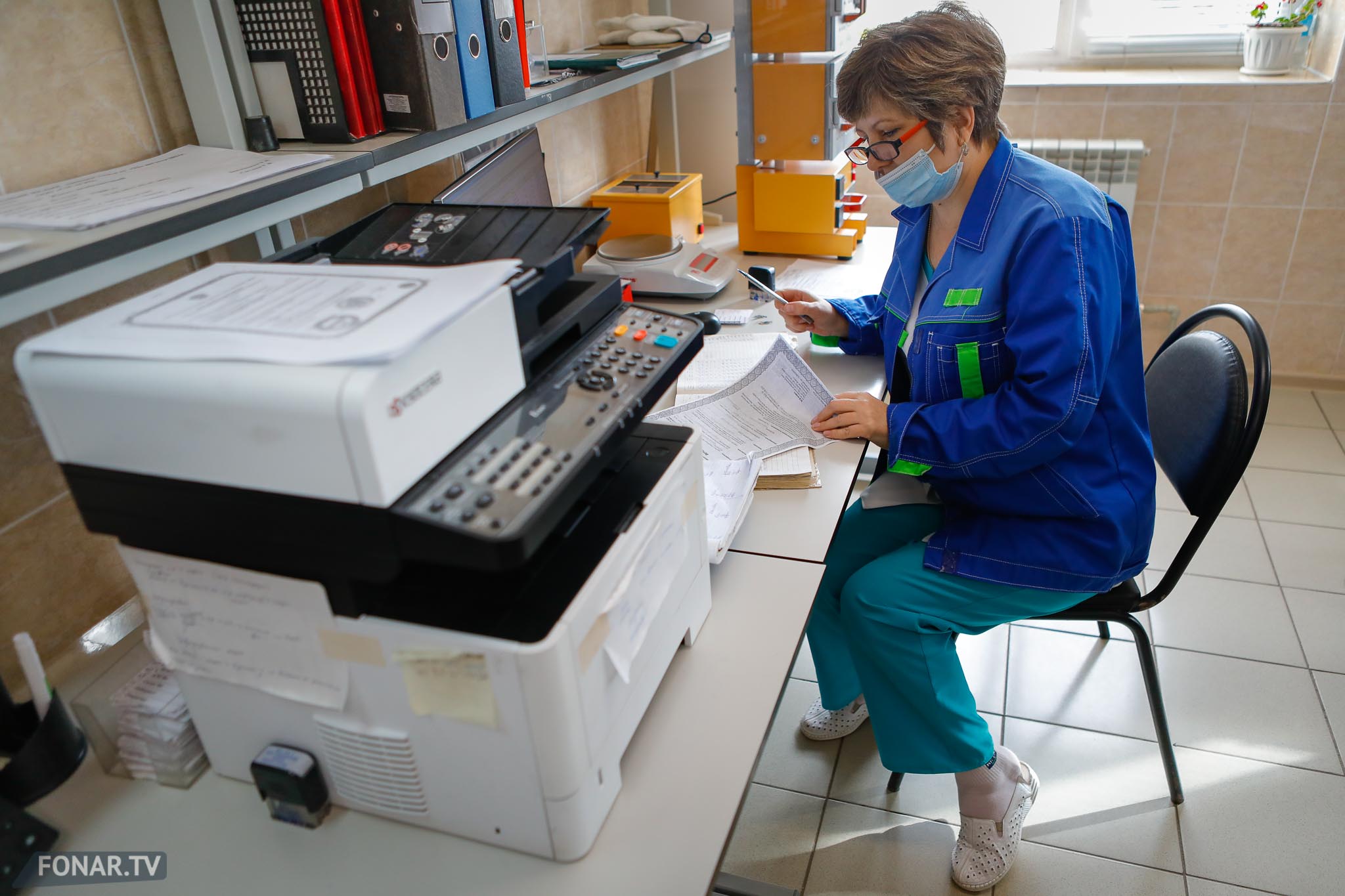

Где хранятся все компоненты
После посещения лаборатории мы проходим на территорию завода — открытую площадку, на которой размещены огромные бочки. Как объясняют сотрудники предприятия, в них хранят сырьё объёмом, которого достаточно для годовой работы завода. Эти бочки называются силосами. В них — горох, кукуруза, жмых, пшеница, ячмень и другое зерновое сырьё. На территории комбикормового завода всего пять силосов, объём каждого из которых достигает 6 тысяч кубических метров.
Всё привозимое на предприятие сырьё ссыпают в завальную яму, откуда потом перемещают на остальные объекты. Загружают его через приёмные устройства, а дальше его перевозят на транспорте и складывают в силос с соответствующим сырьём.
Следующая точка нашей экскурсии — склад хранения тарного зерна, которое нужно для производства комбикорма. Его привозят автотранспортом, потом размещают на складе. Чтобы завод в течении суток мог производить комбикорм, необходимо заполнить все внутренние бункеры. Всего их на предприятии 21: 11 бункеров крупного дозирования по 30-60 тонн, а 10 — мелкого дозирования по одной-три тонны. В крупные бункера насыпают зерно или высокобелковое сырьё, в мелкие — известняк, метионин, премиксы и другие кислоты и аминокислоты. Всего в комбикорм входит более 30 различных компонентов.
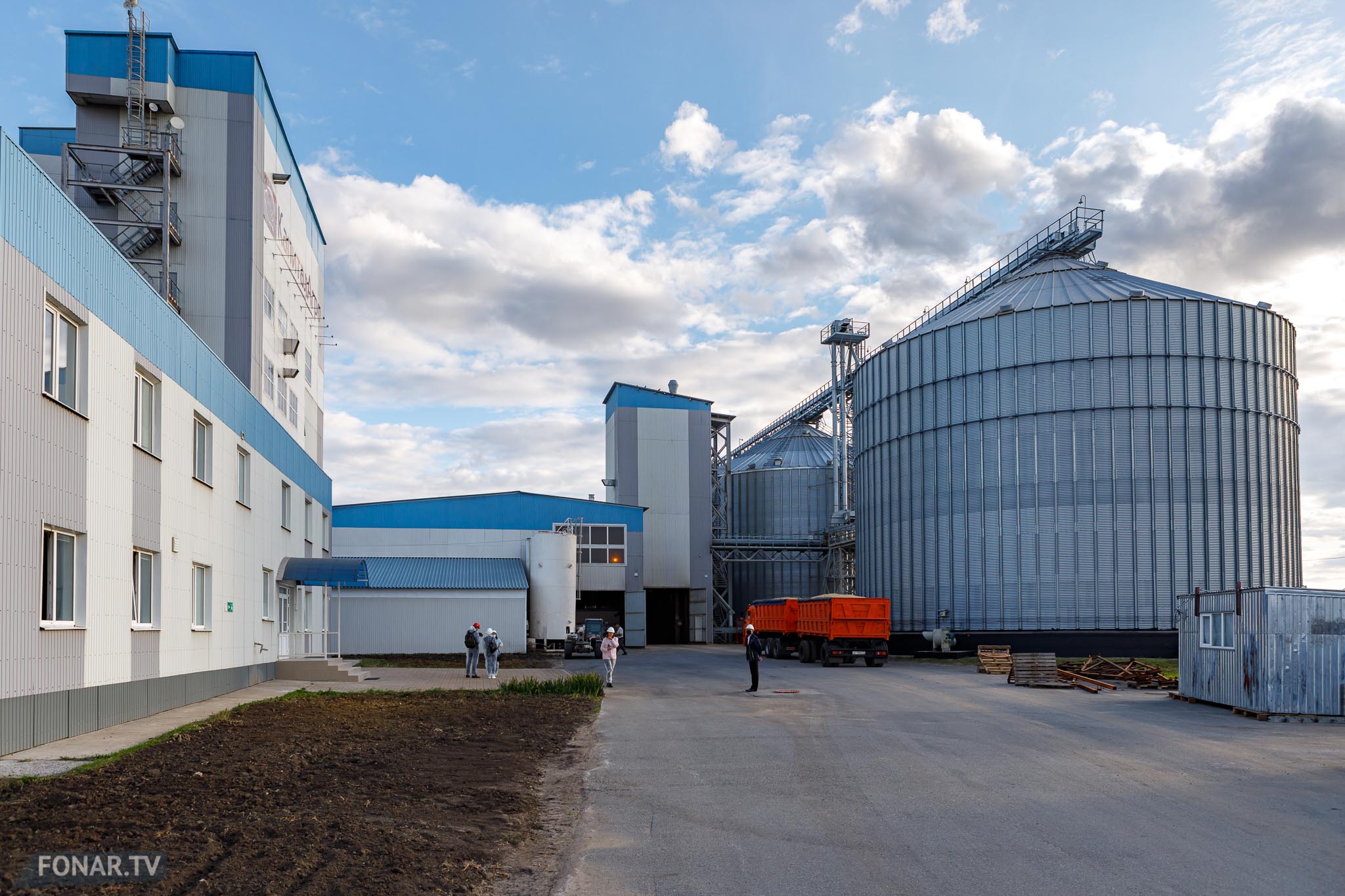
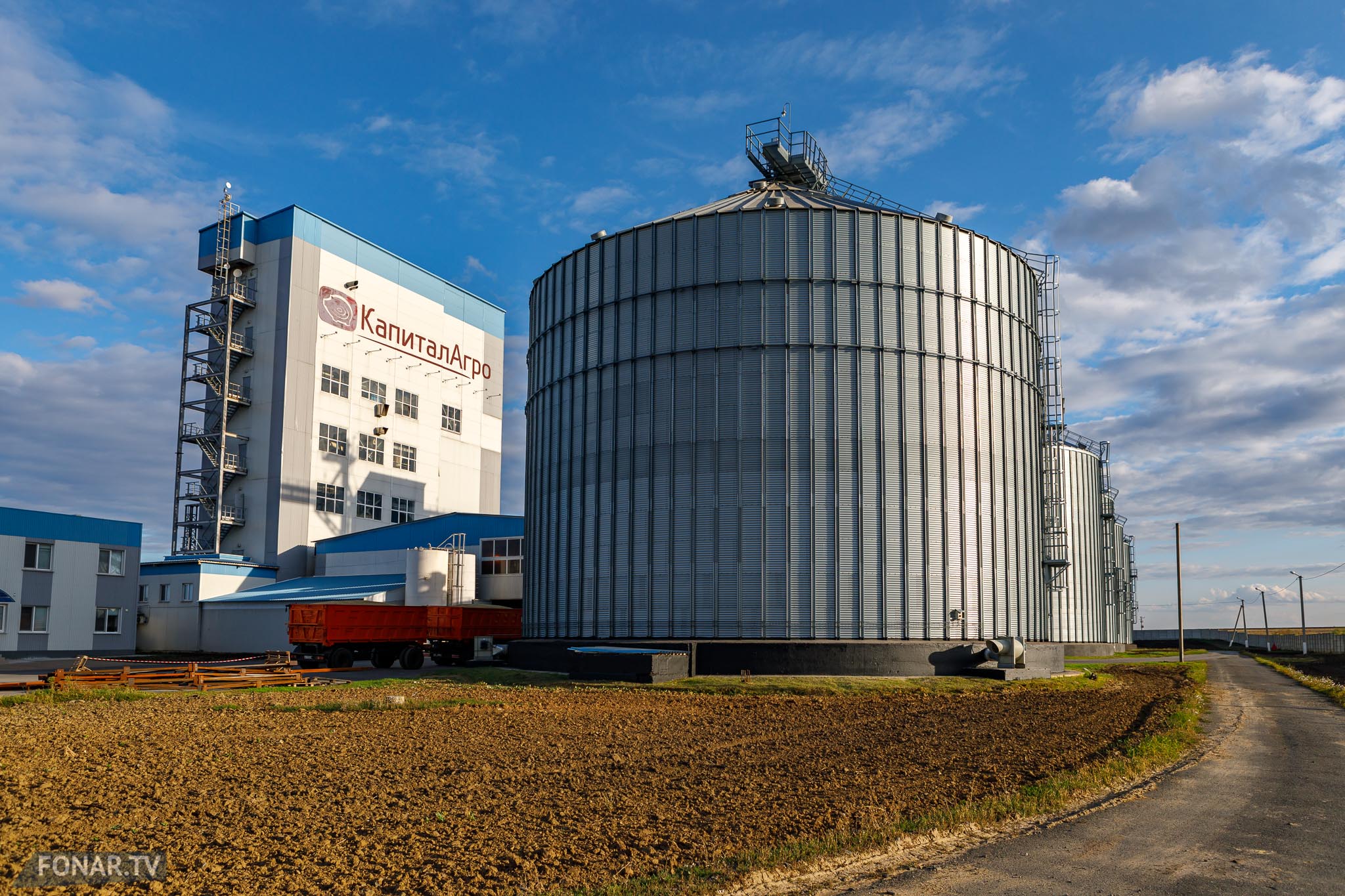
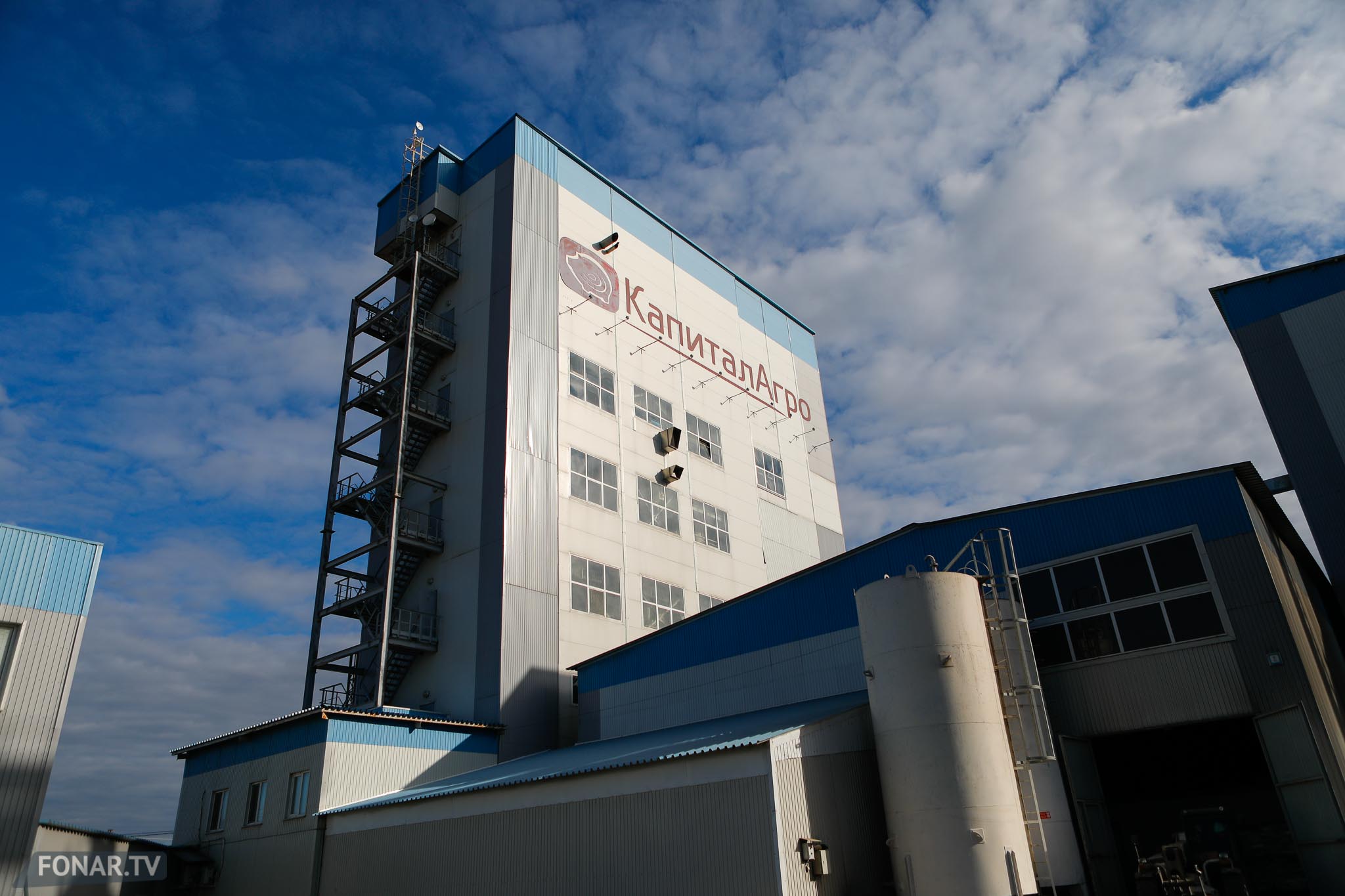
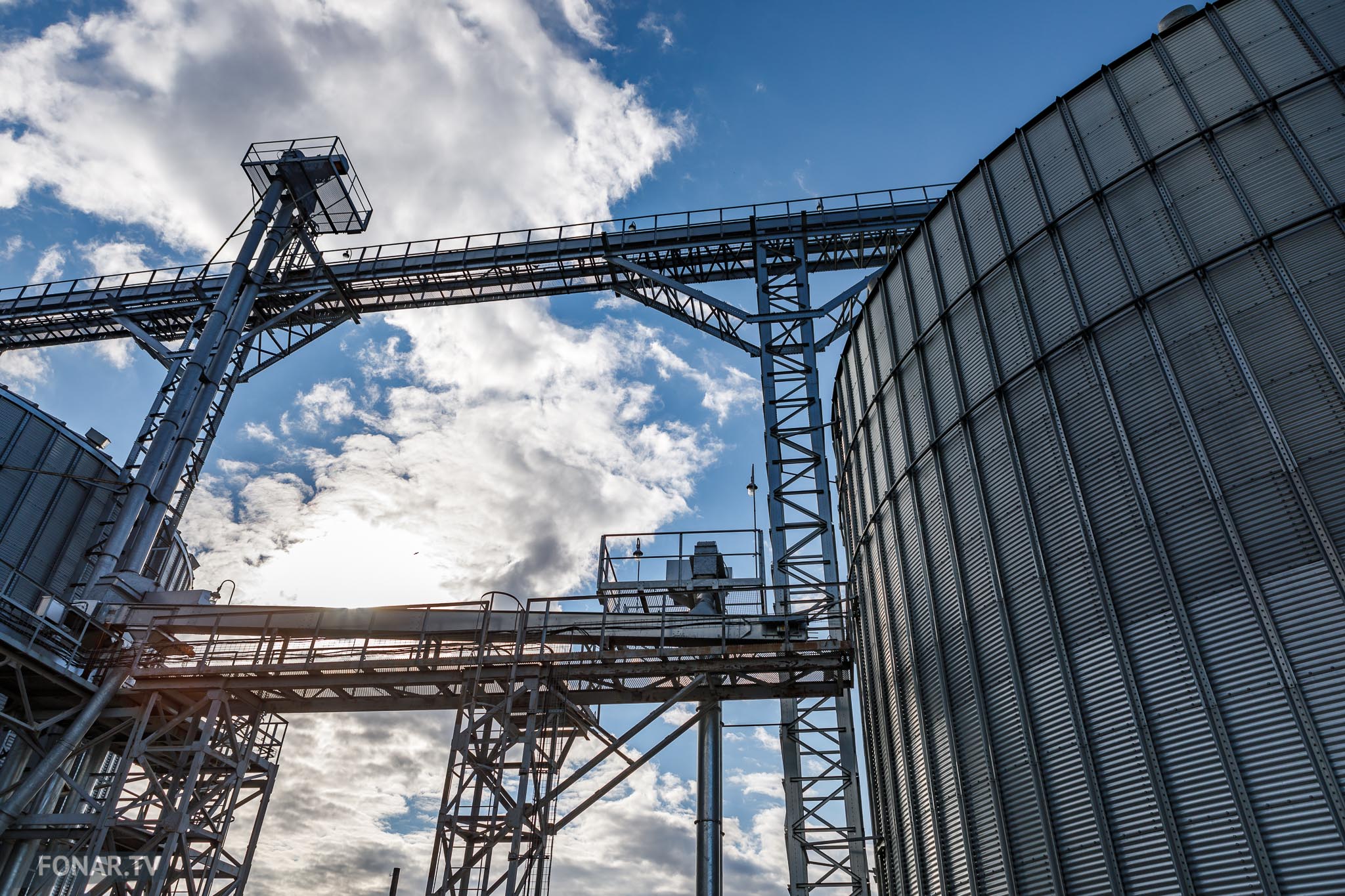
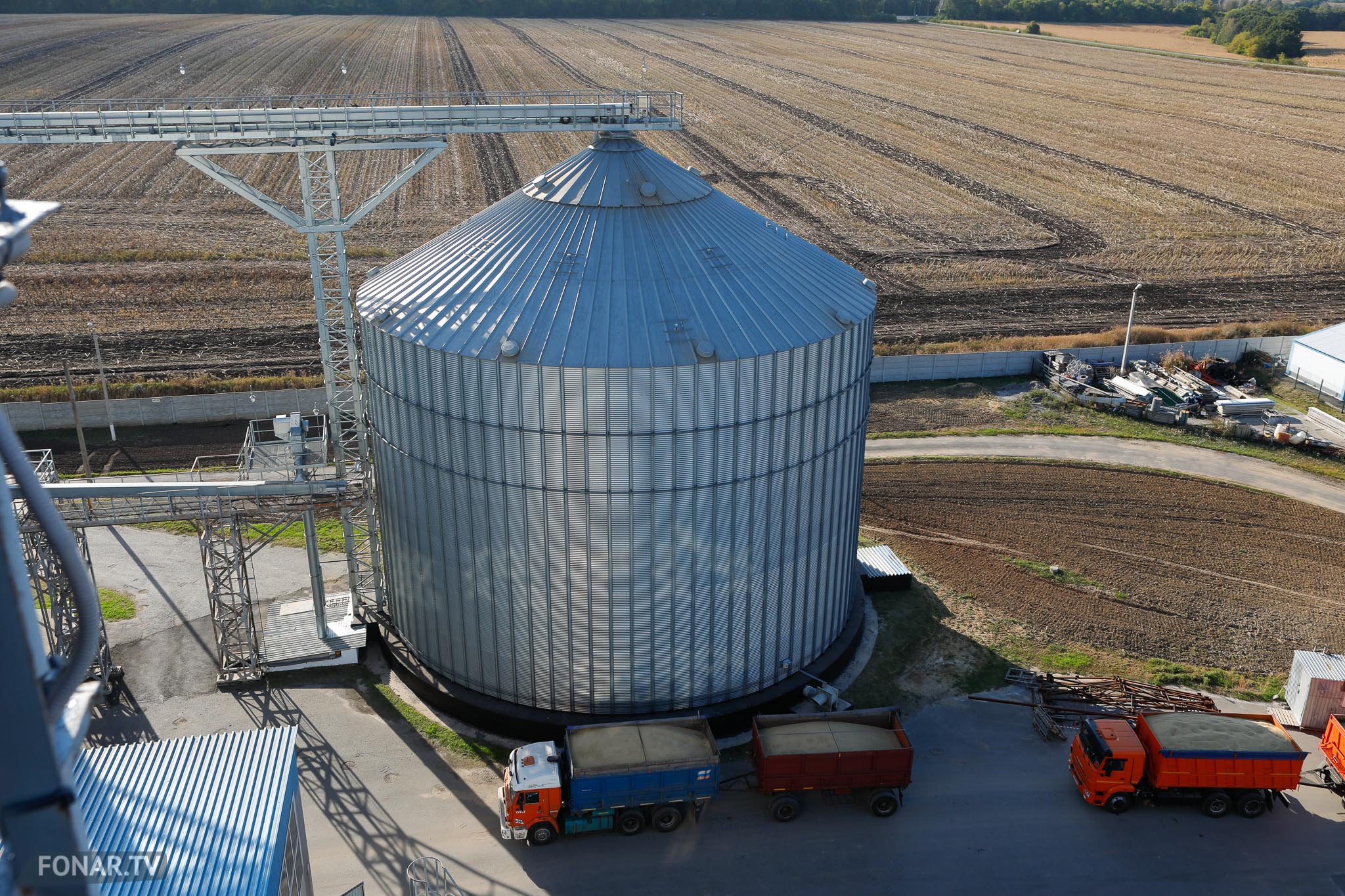
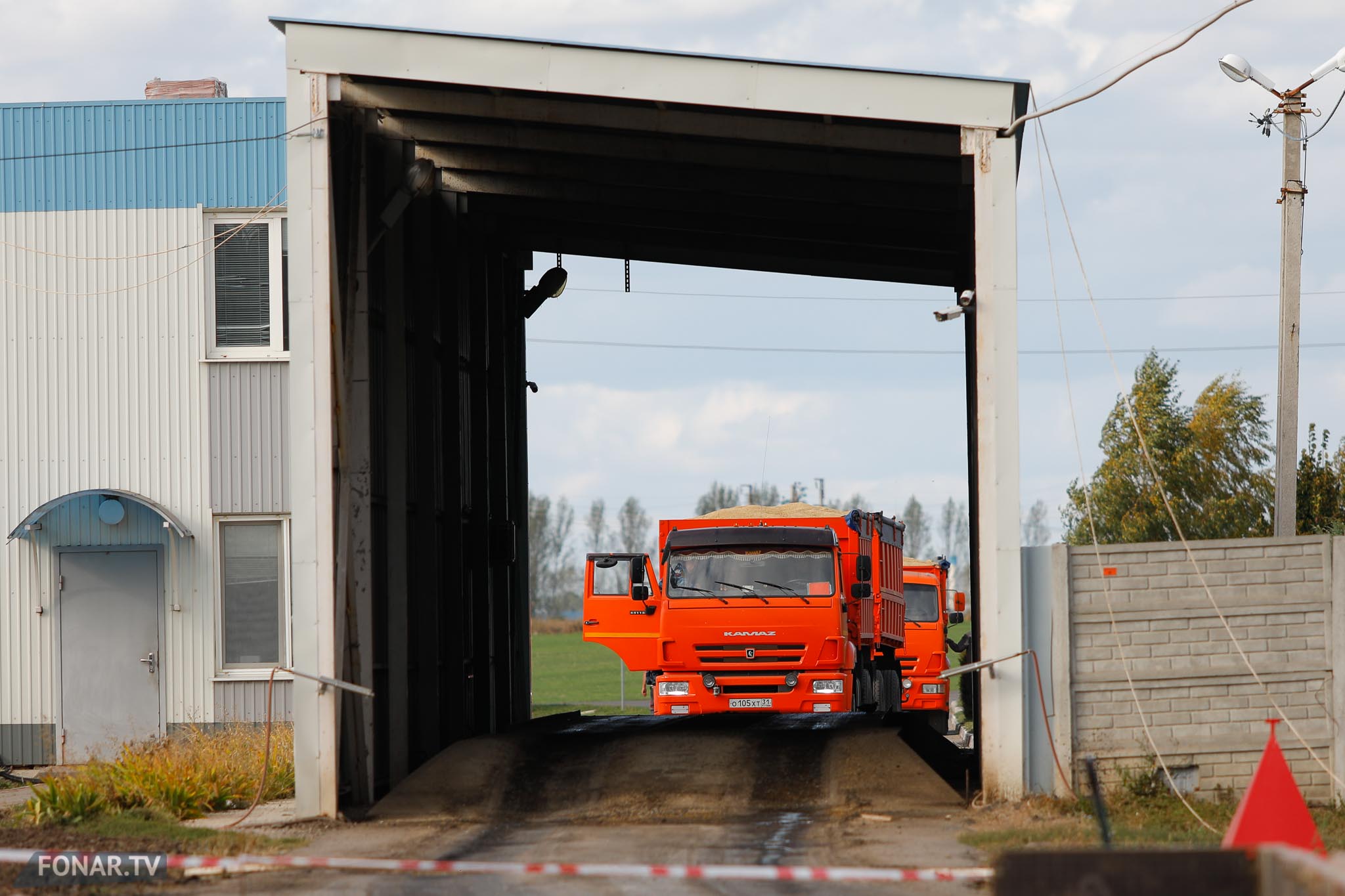
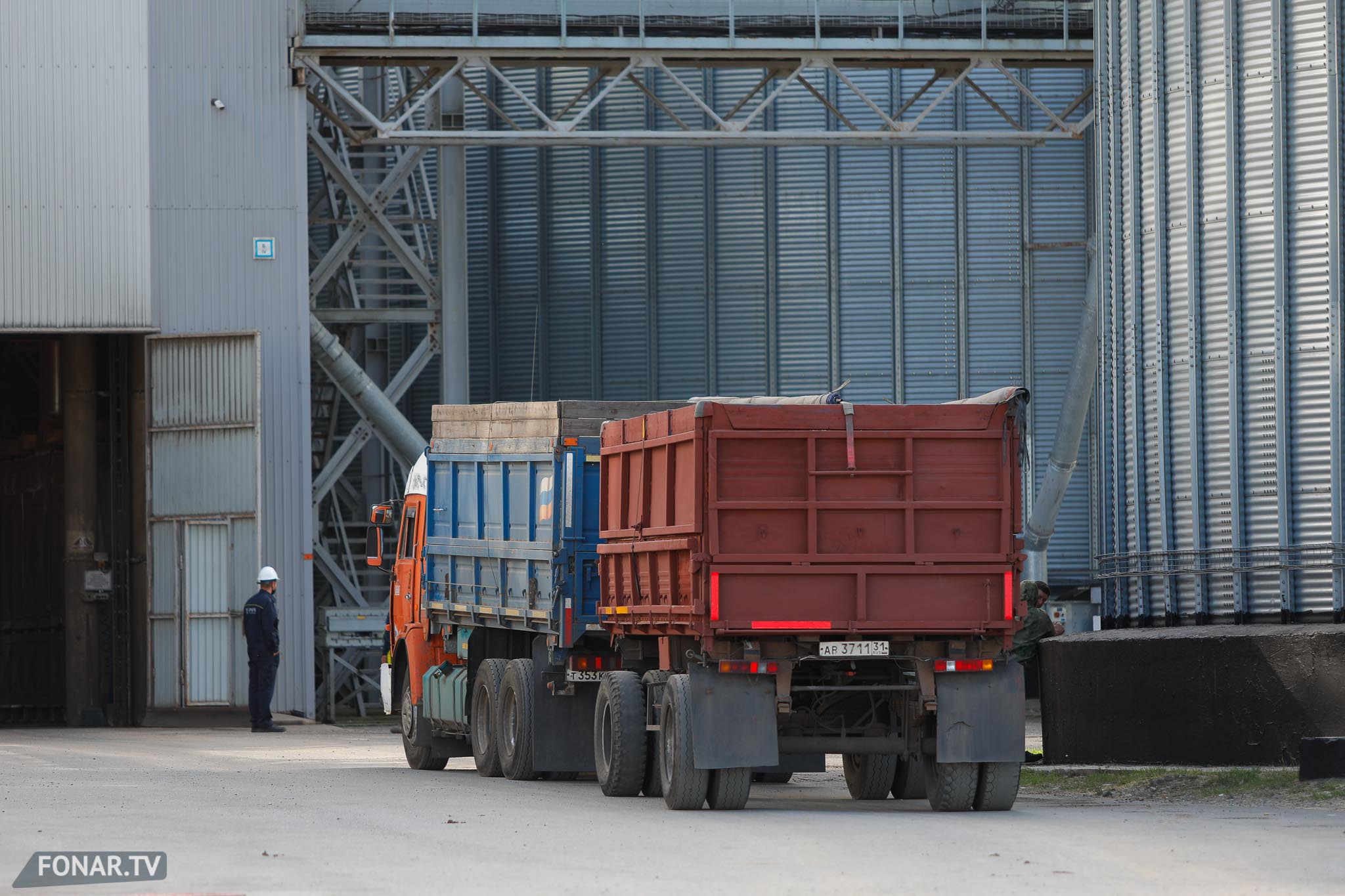
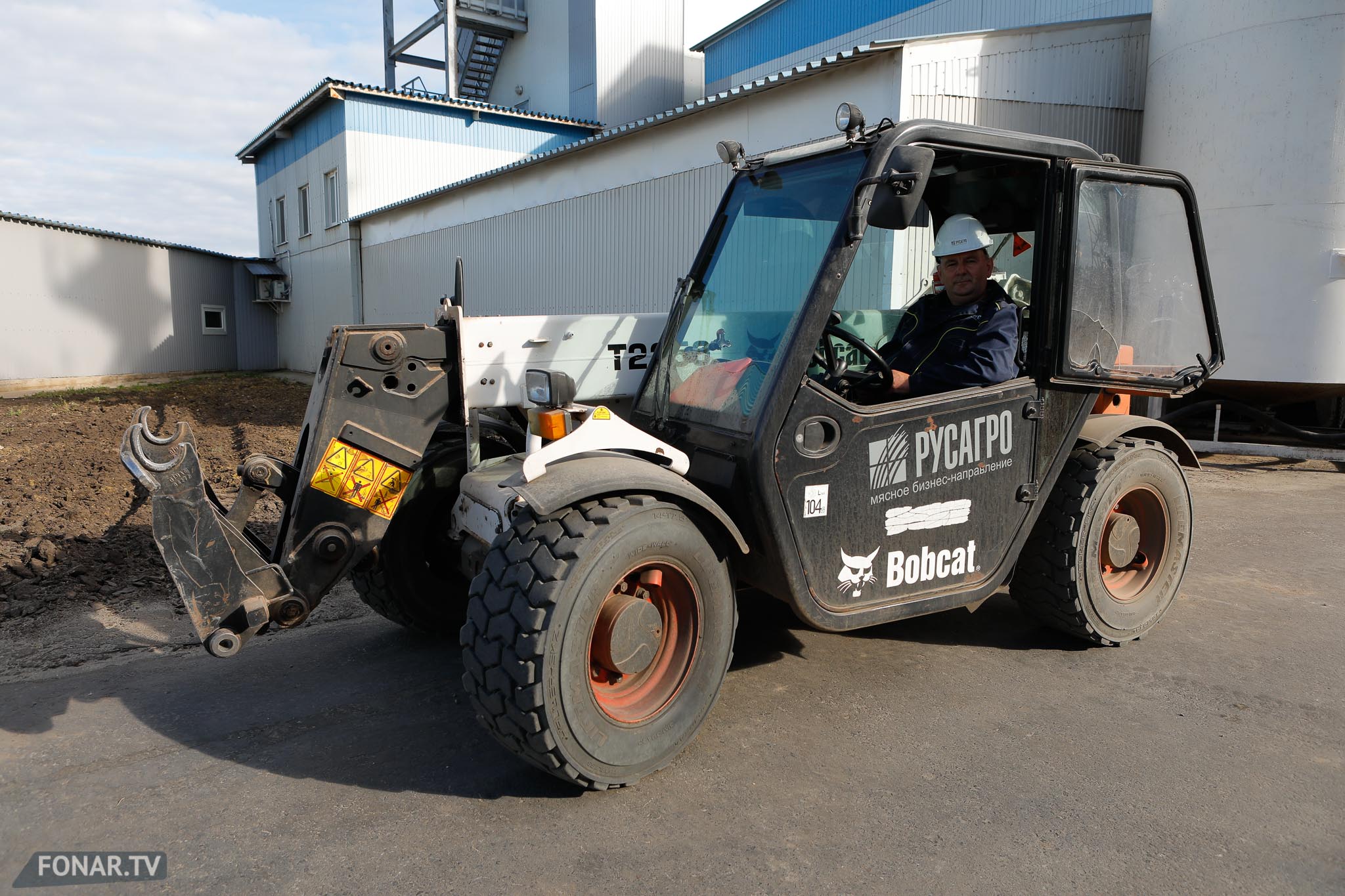
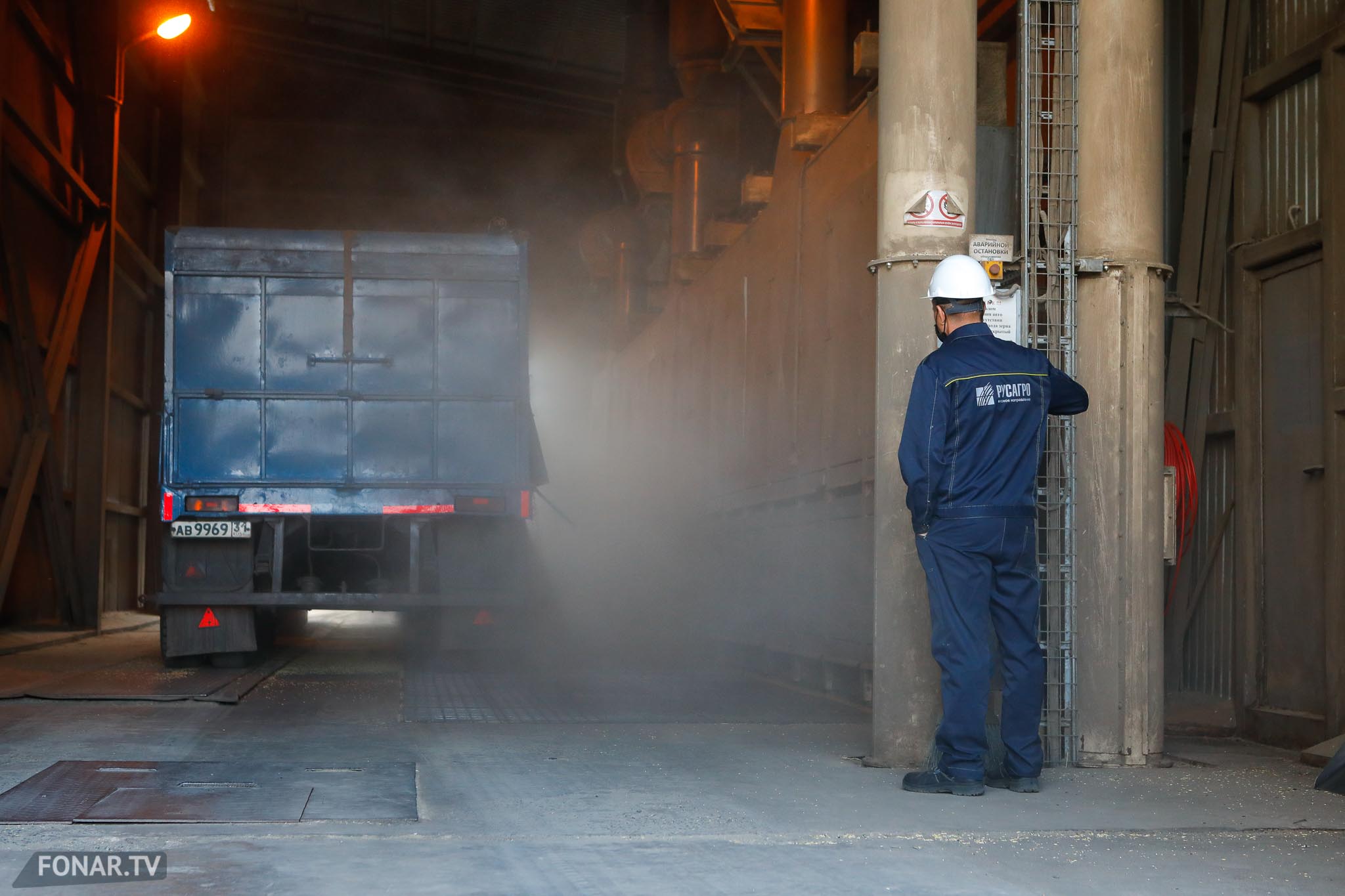
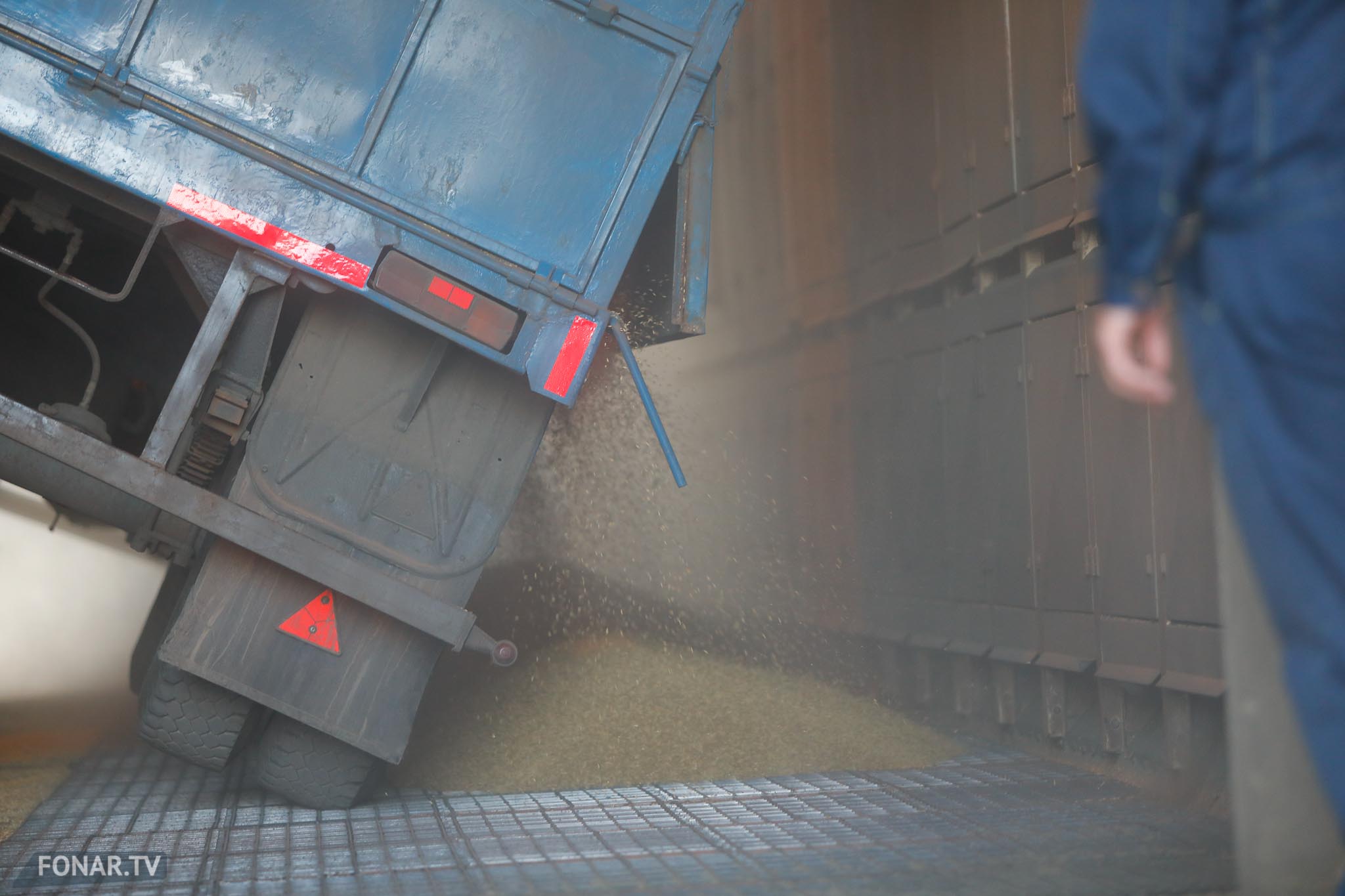
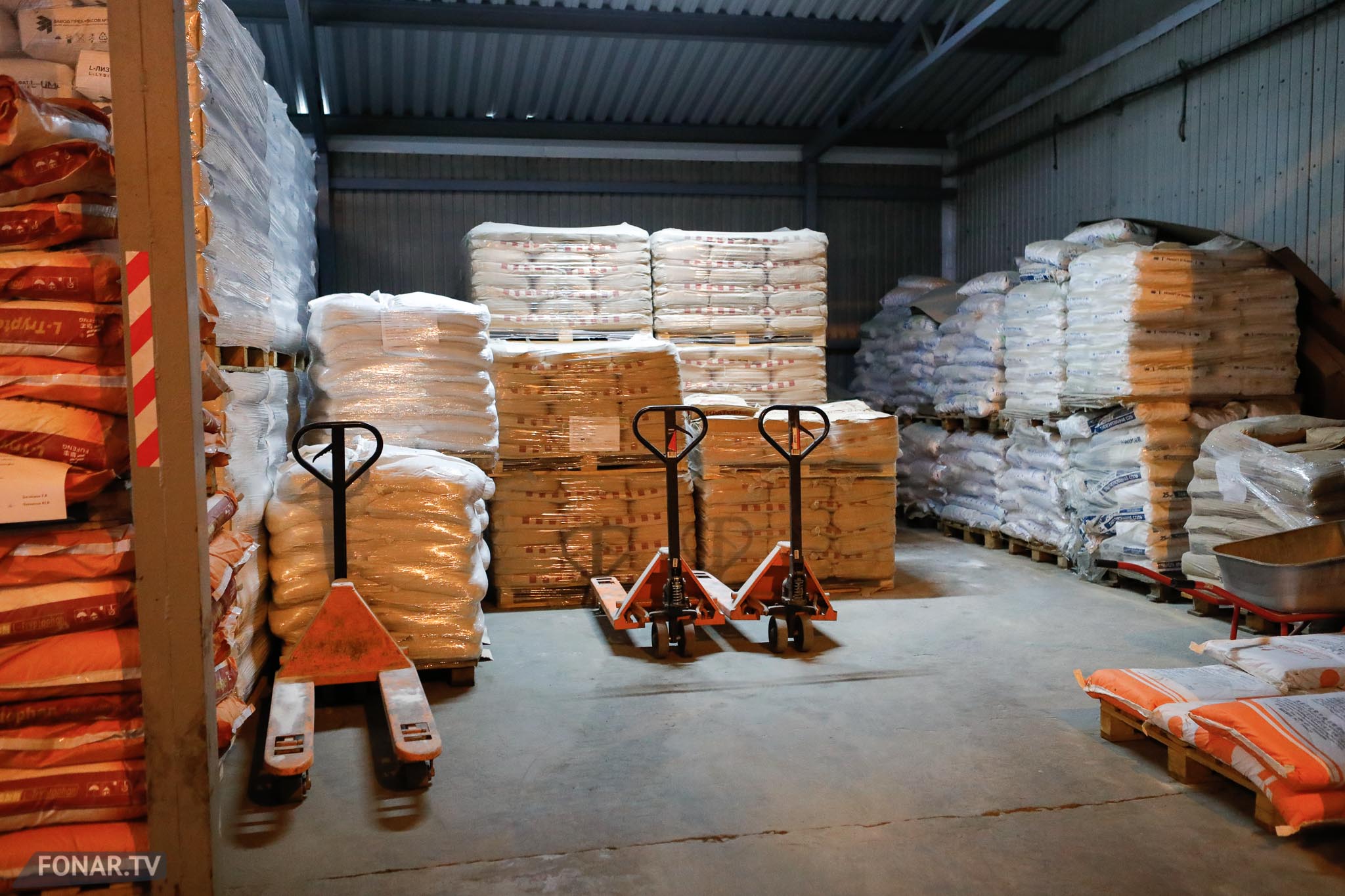
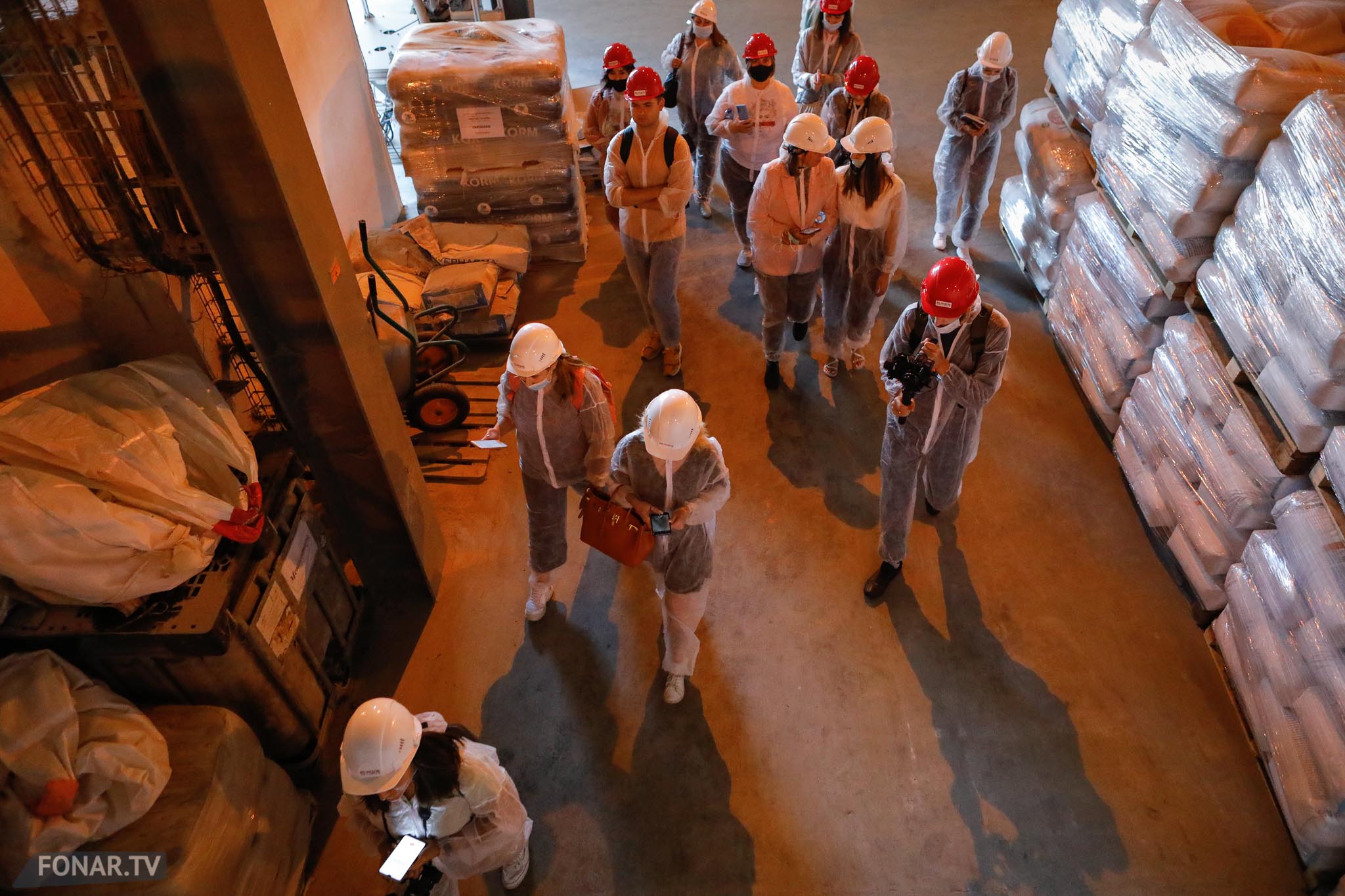
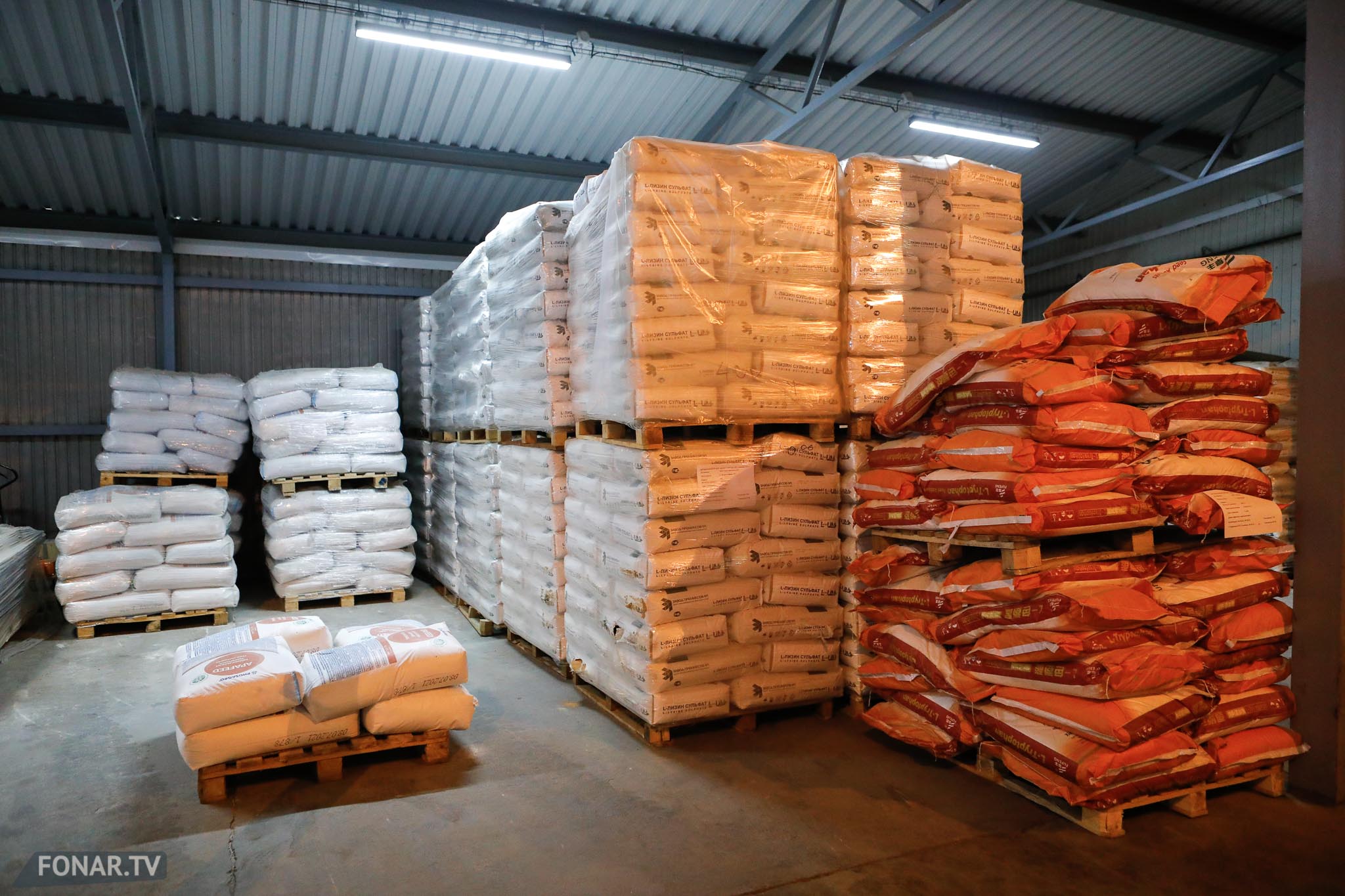
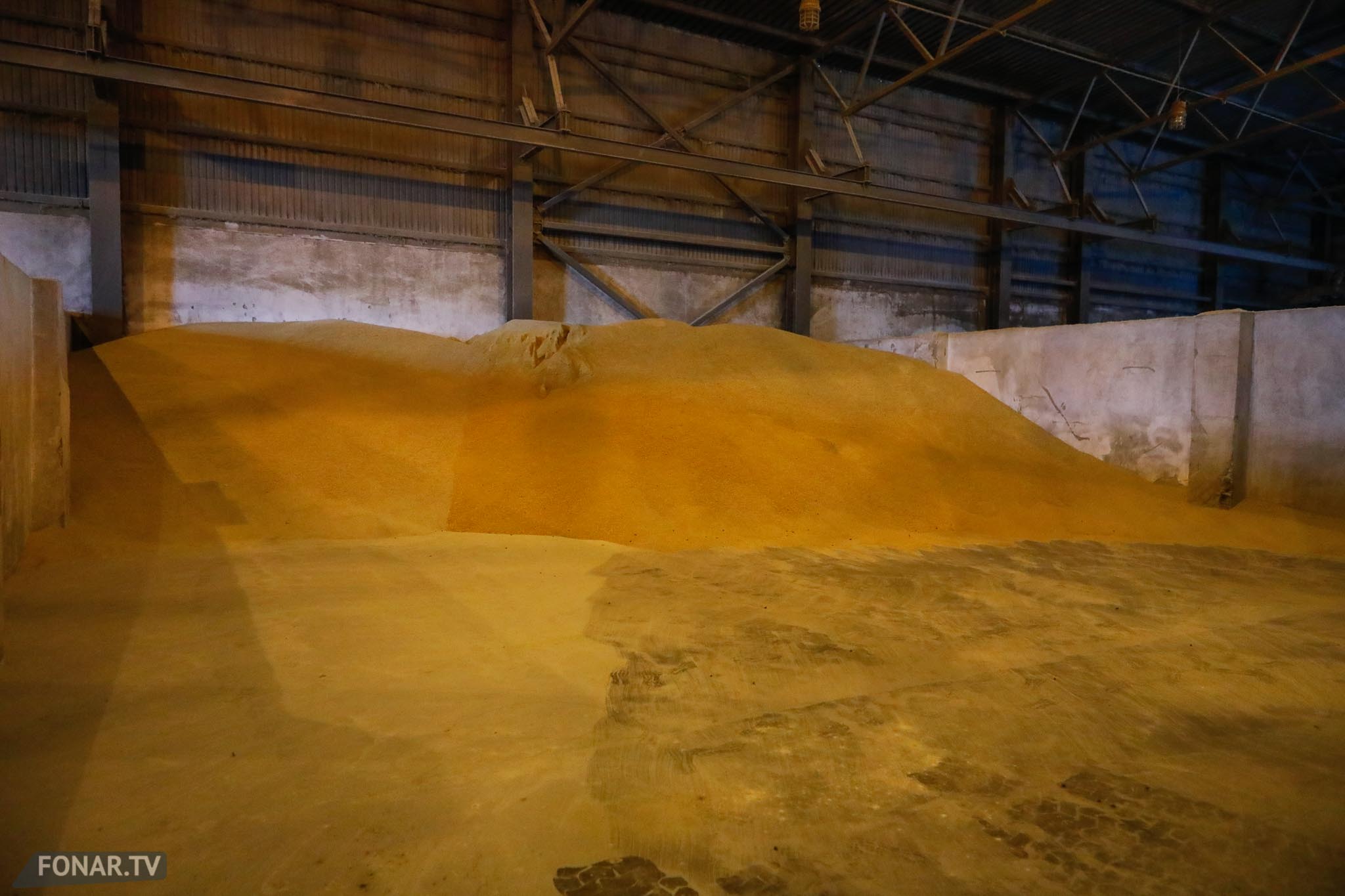
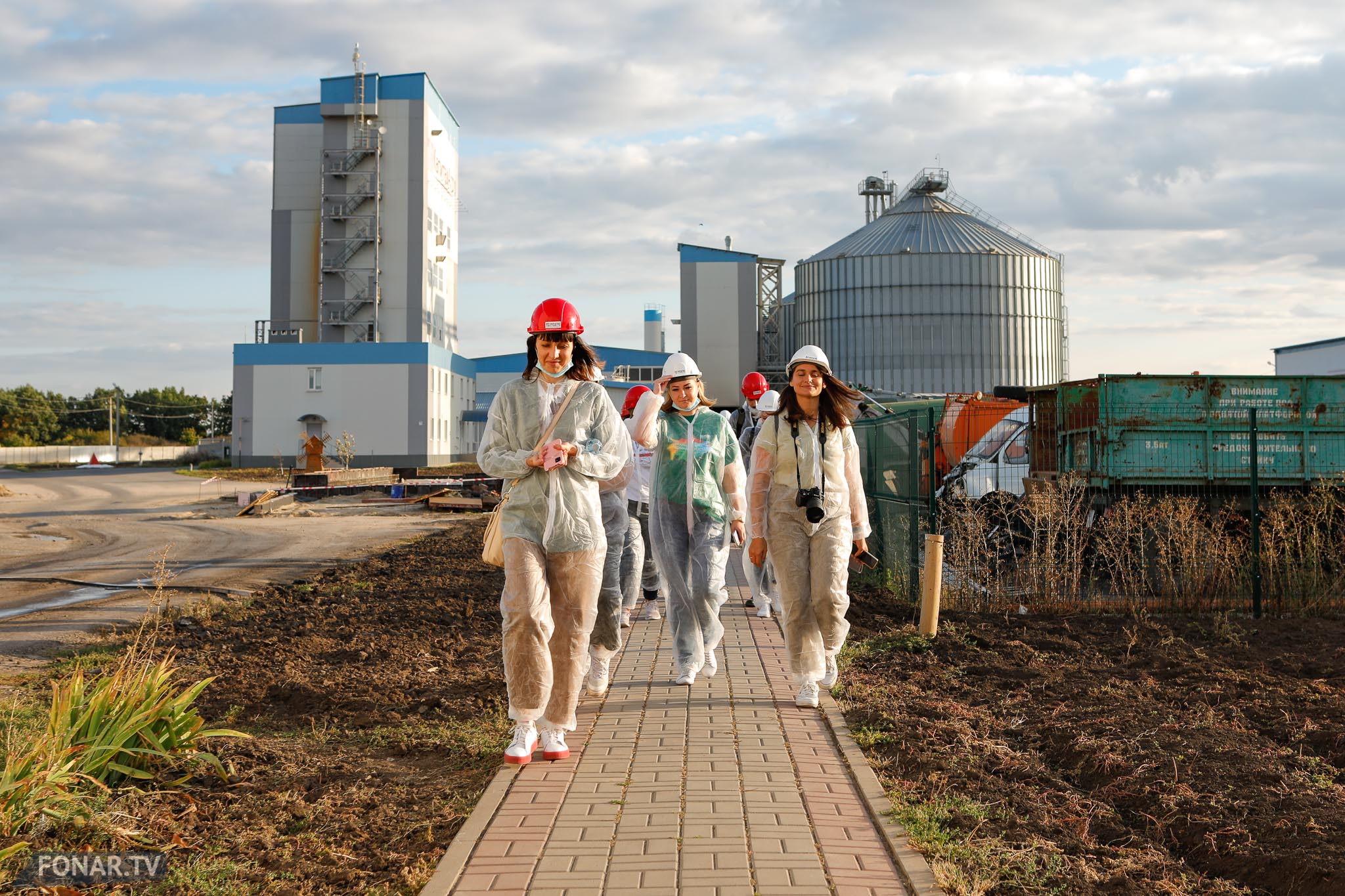
Кстати, иногда остатки чипсов, сухариков и кукурузных палочек тоже могут идти в корма. Их используют в рецептуре, так как они богаты крахмалом и недорого стоят.
— Перемещается сырьё в бункеры для того, чтобы автоматизированное оборудование дозировало его на весы и в течение суток производило без остановки комбикорм. На следующие сутки нужно опять загружать бункеры всеми компонентами. Задача производства — держать их полными, чтобы не остановить работу завода из-за отсутствия того или иного компонента. Далее сырьё подаётся на седьмой этаж и разделяется по компонентам. Высокобелковое сырьё (например, жмых подсолнечный) хранится в секциях, подаётся из транспортного оборудования (наверху есть транспортёр, который поставляется на той или иной бокс). Та завальная яма, что мы видели, тоже может принимать это сырьё, и аппаратура перемещает её в необходимые места, — рассказал инженер комбикормового завода Сергей Стронин.
Как из кукурузы и жмыха получается корм
Мы переходим в производственный семиэтажный корпус завода. Здесь есть грузовой лифт, на котором можно доставить необходимые компоненты на любой этаж. Для сотрудников завода есть ещё один способ перемещаться по отделениям — лестница на улице, которую построили рядом с производственным корпусом. Тут же с неё на последнем этаже, который находится в 27,5 метрах от земли, открывается красивый вид на площадку.
Перейдём к принципам работы завода. Привозимое сырьё поднимается наверх, а потом с помощью специальных ковшей его сбрасывают вниз. Таким образом оно горизонтально попадает в бункеры крупного дозирования, то есть каждое сырьё имеет свой отдельный путь. После этого, смотря какой задан рецепт, сырьё дозируется на весы — это происходит автоматически по очереди. Каждый компонент насыпается в определённом количестве в определённой последовательности.
После взвешивания одной пропорции, которая составляет две тонны, сырьё падает вниз и поднимается опять наверх на транспорте. Потом его опускают вниз и отправляют в дробилку. Далее через смеситель, в котором сырьё встречается с микрокомпонентами, всю эту массу смешивают. Получается уже почти готовый комбикорм, только негранулированный. Теоретически, его уже можно отдавать на корм скоту, только перед этим необходимо обработать паром, чтобы убить все болезнетворные бактерии и вирусы.
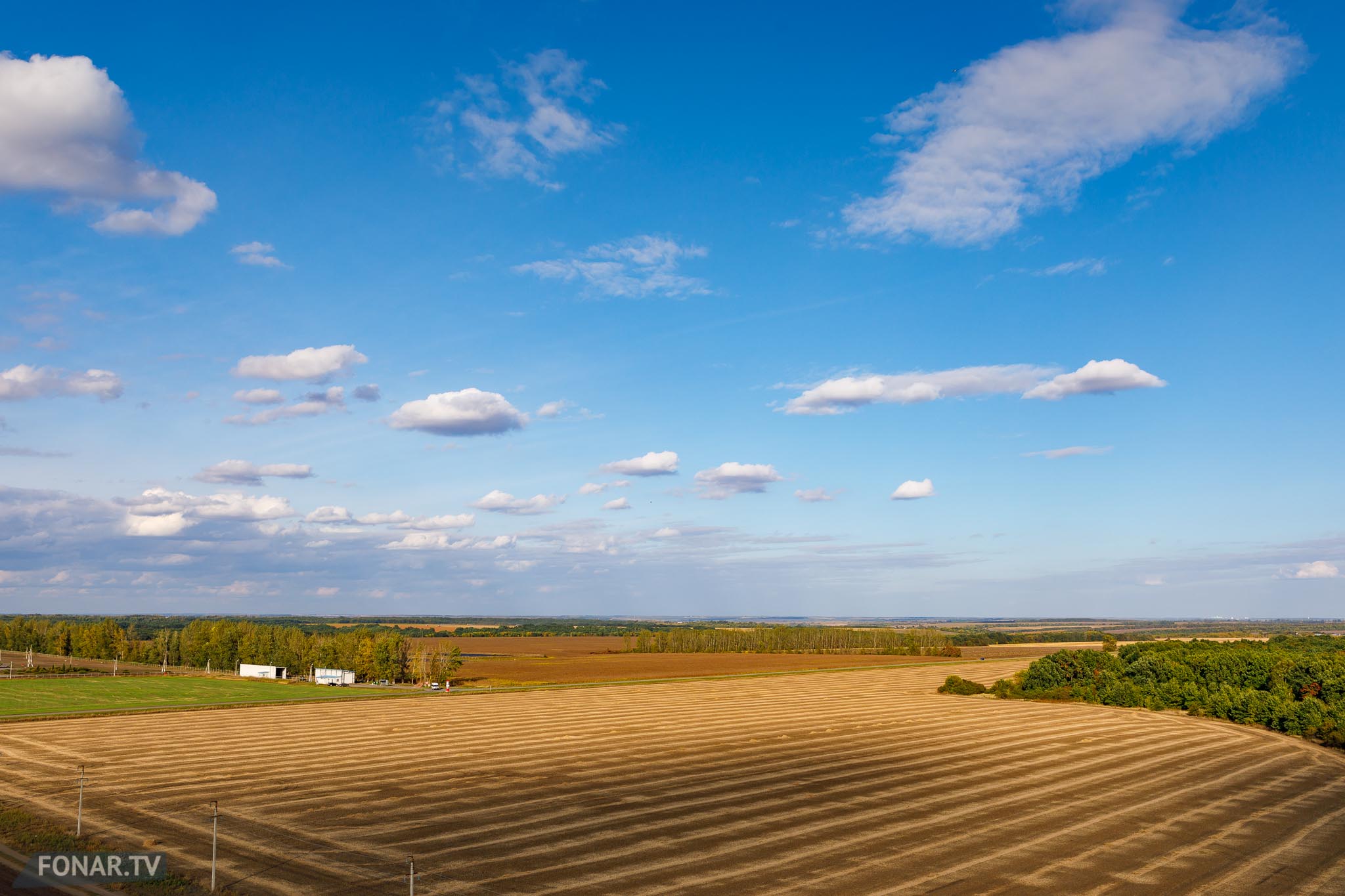
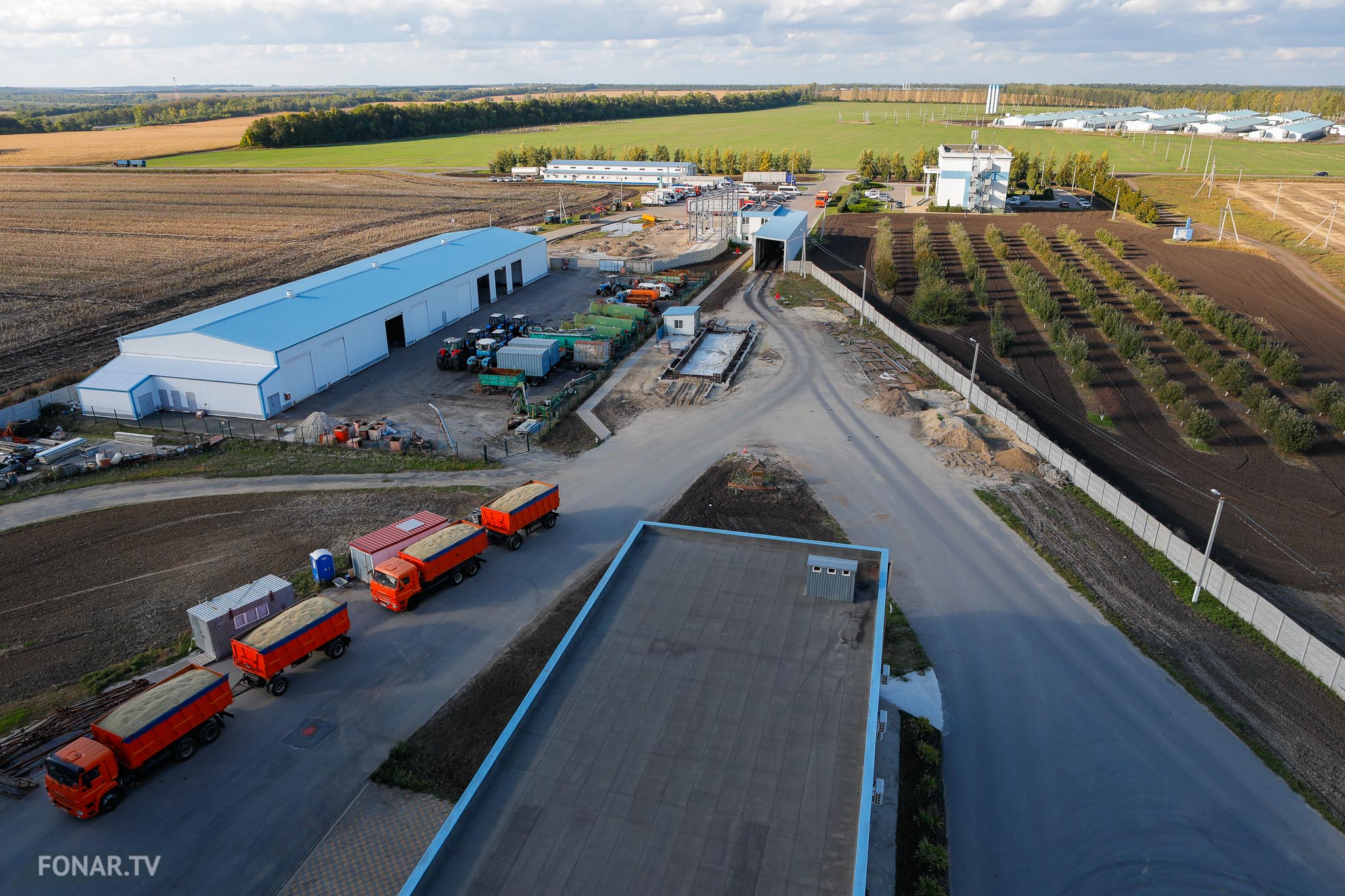
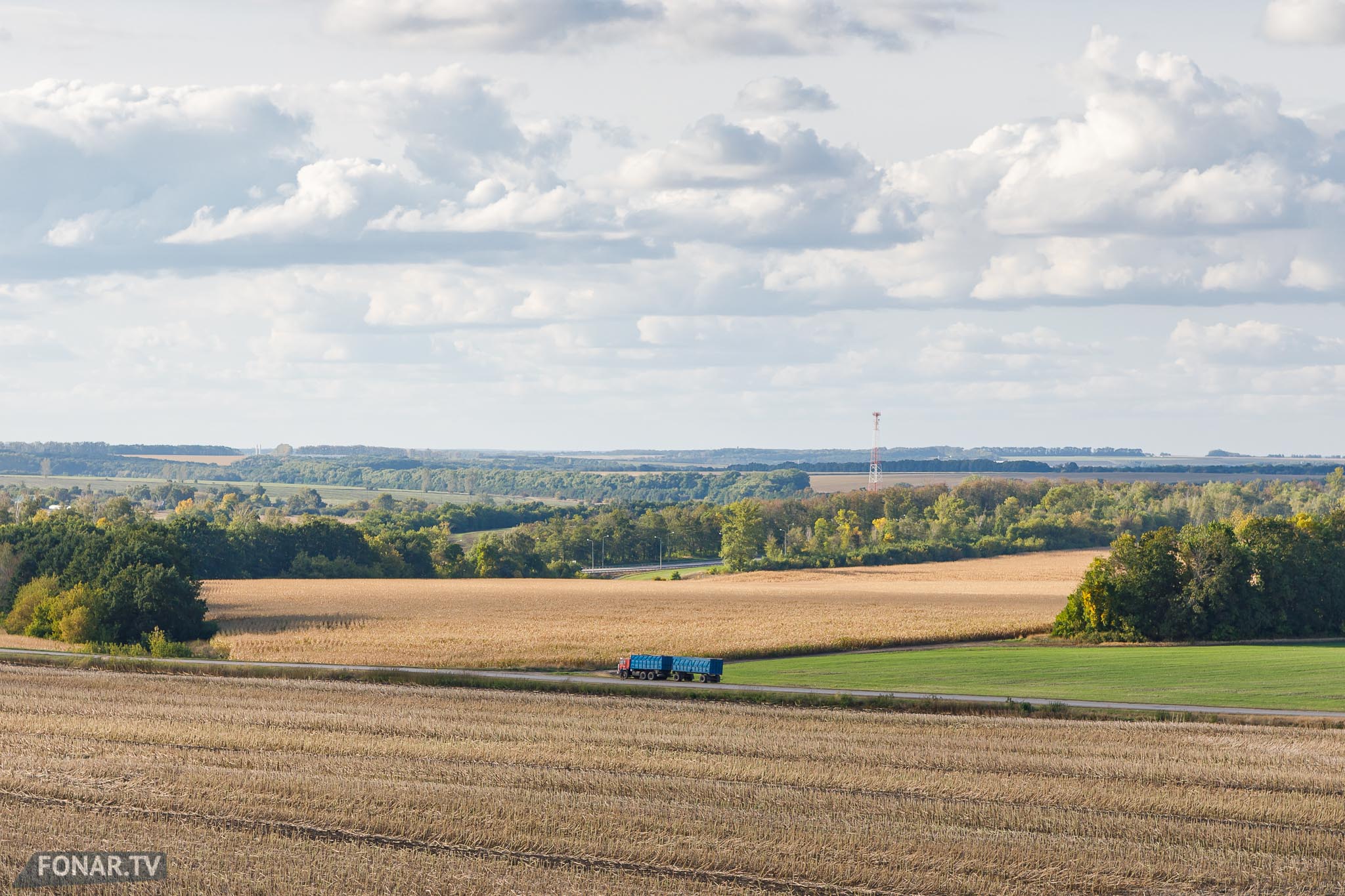
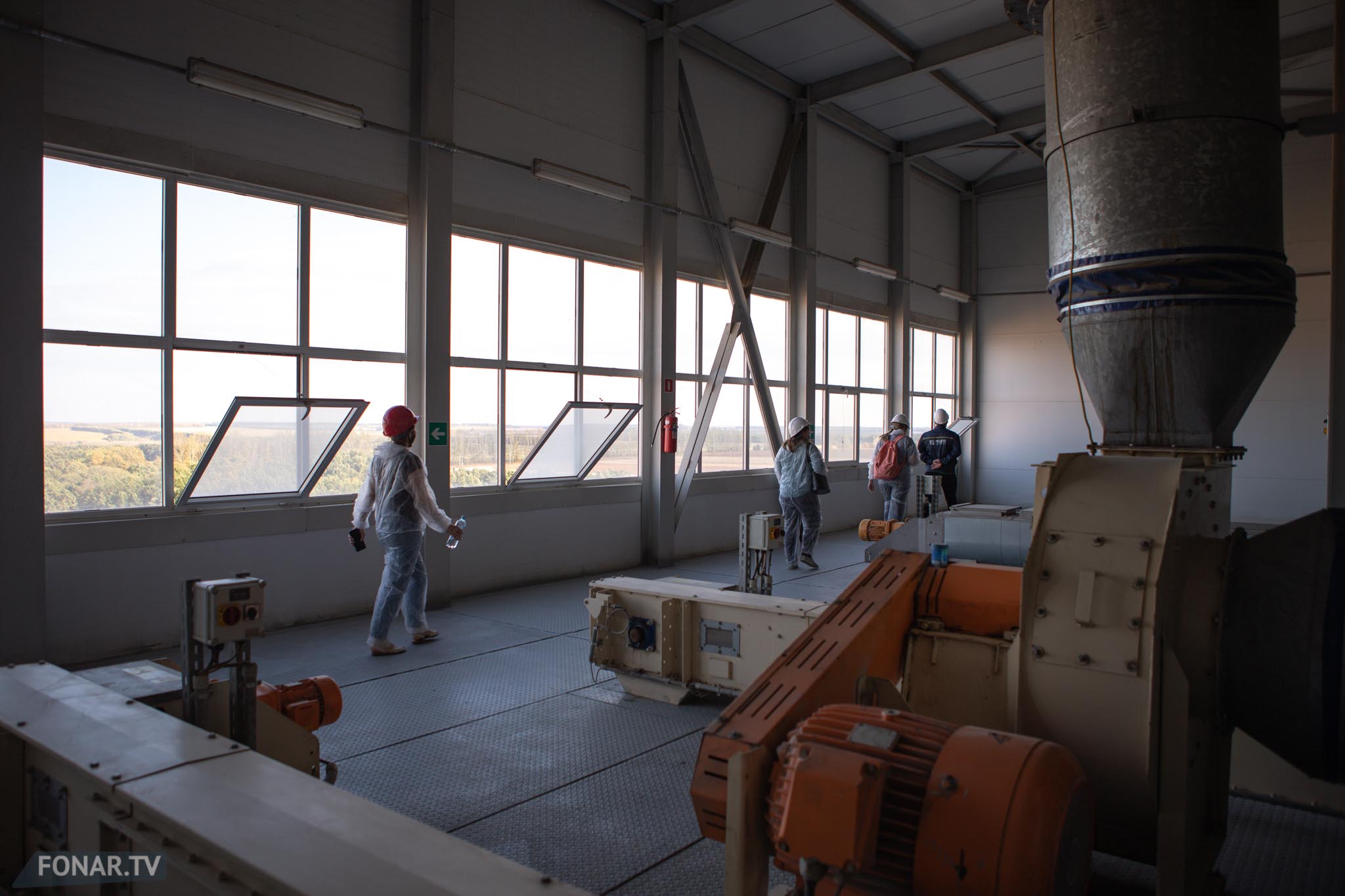
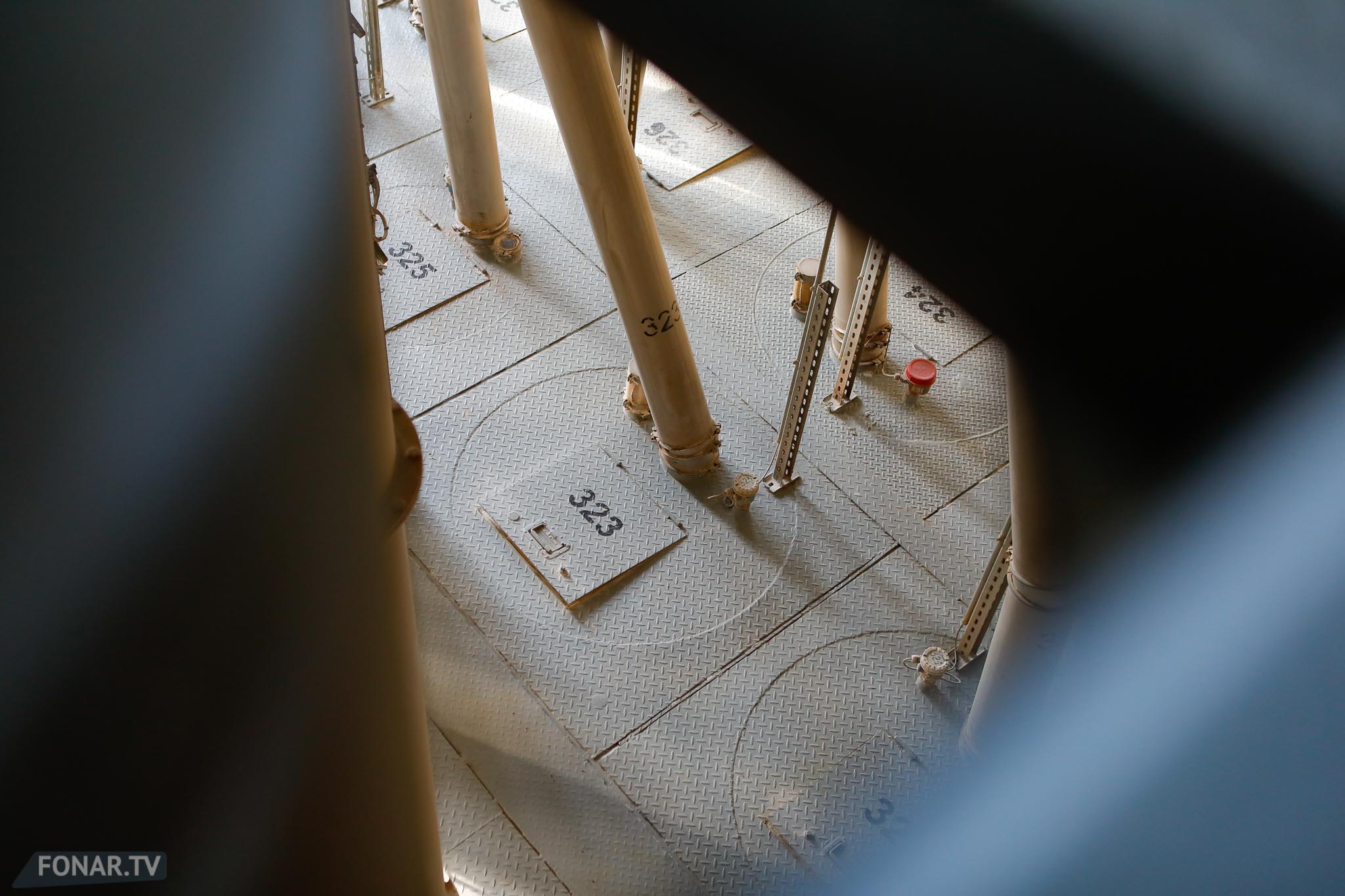
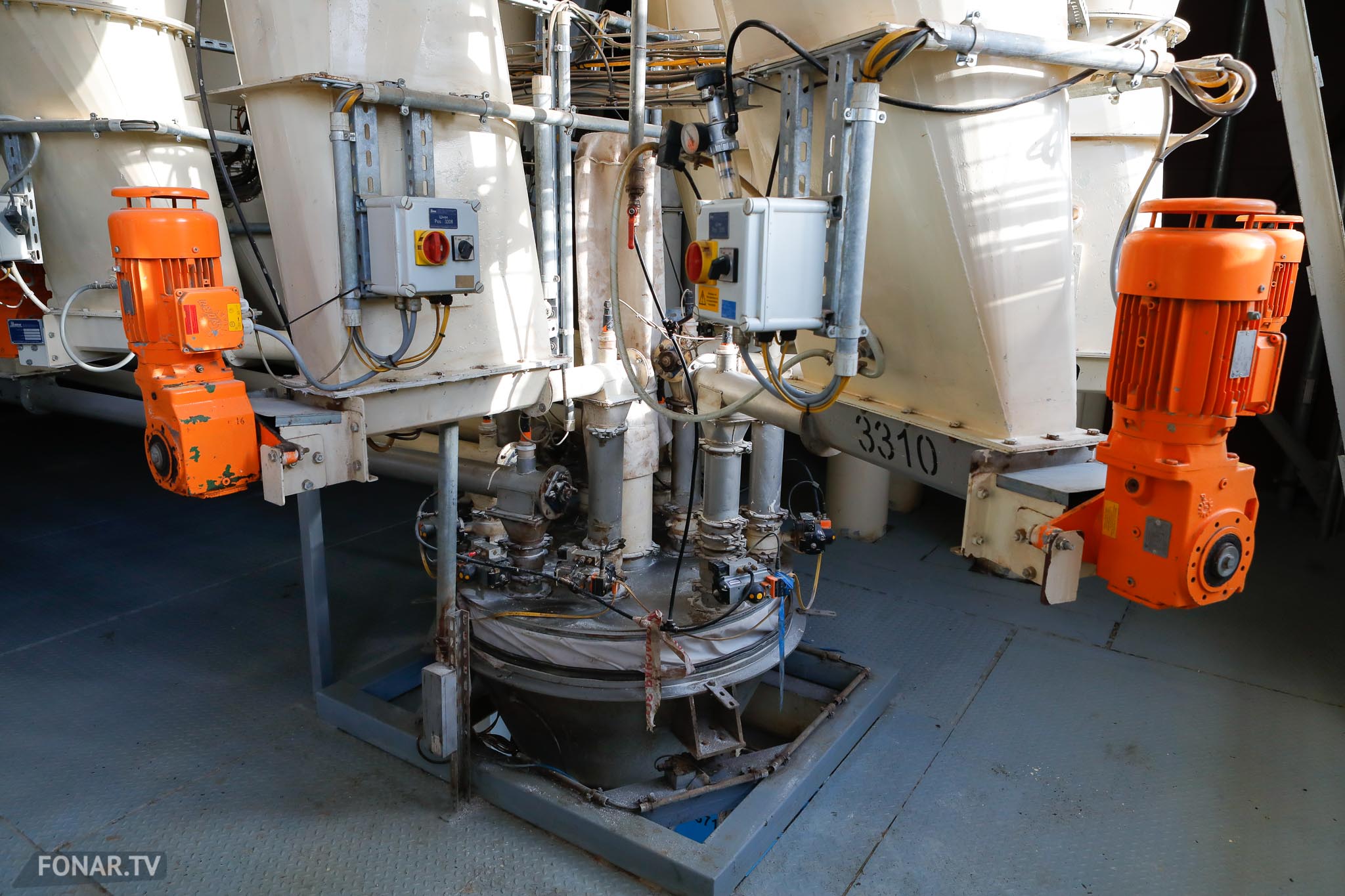
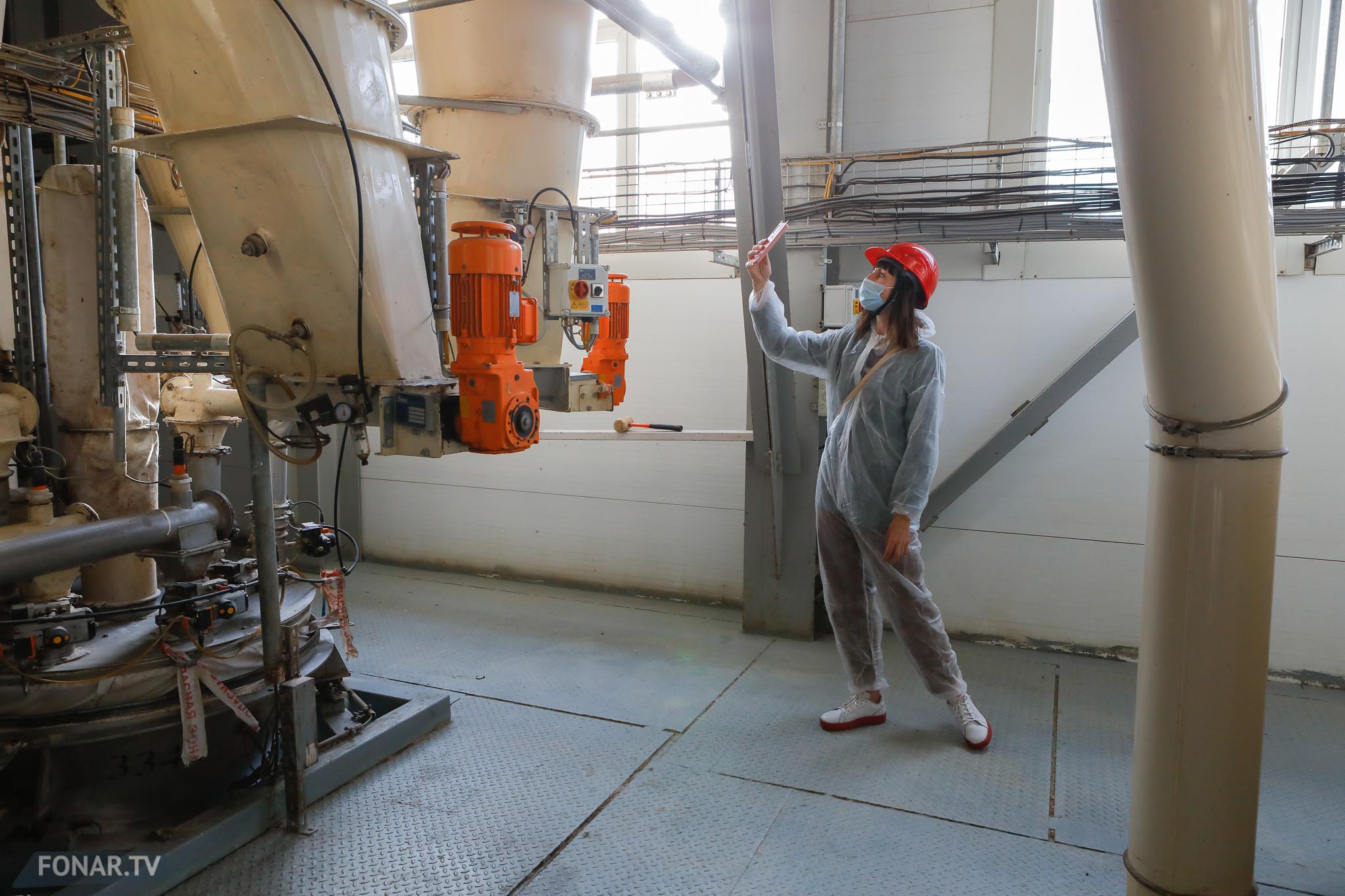
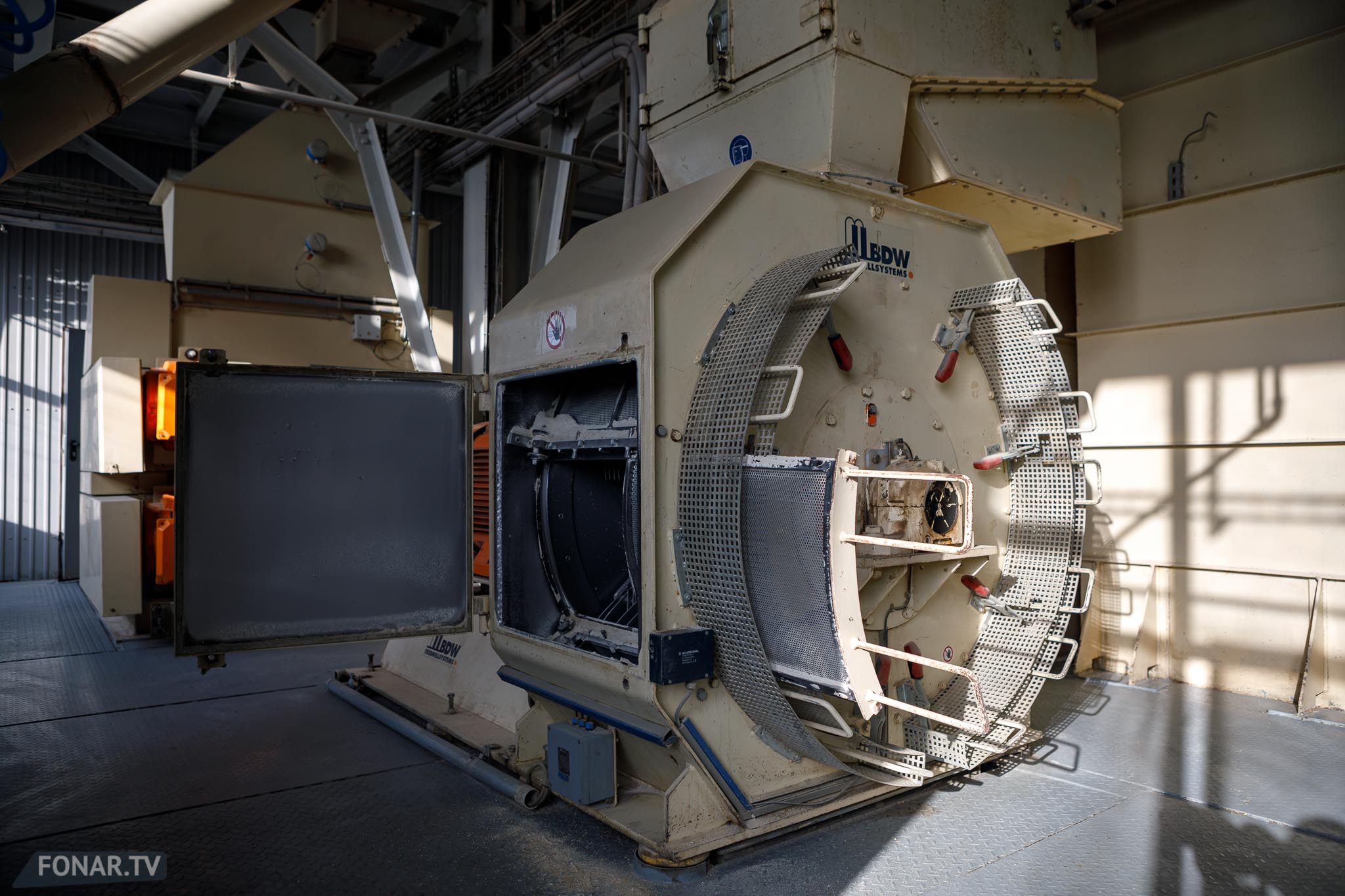
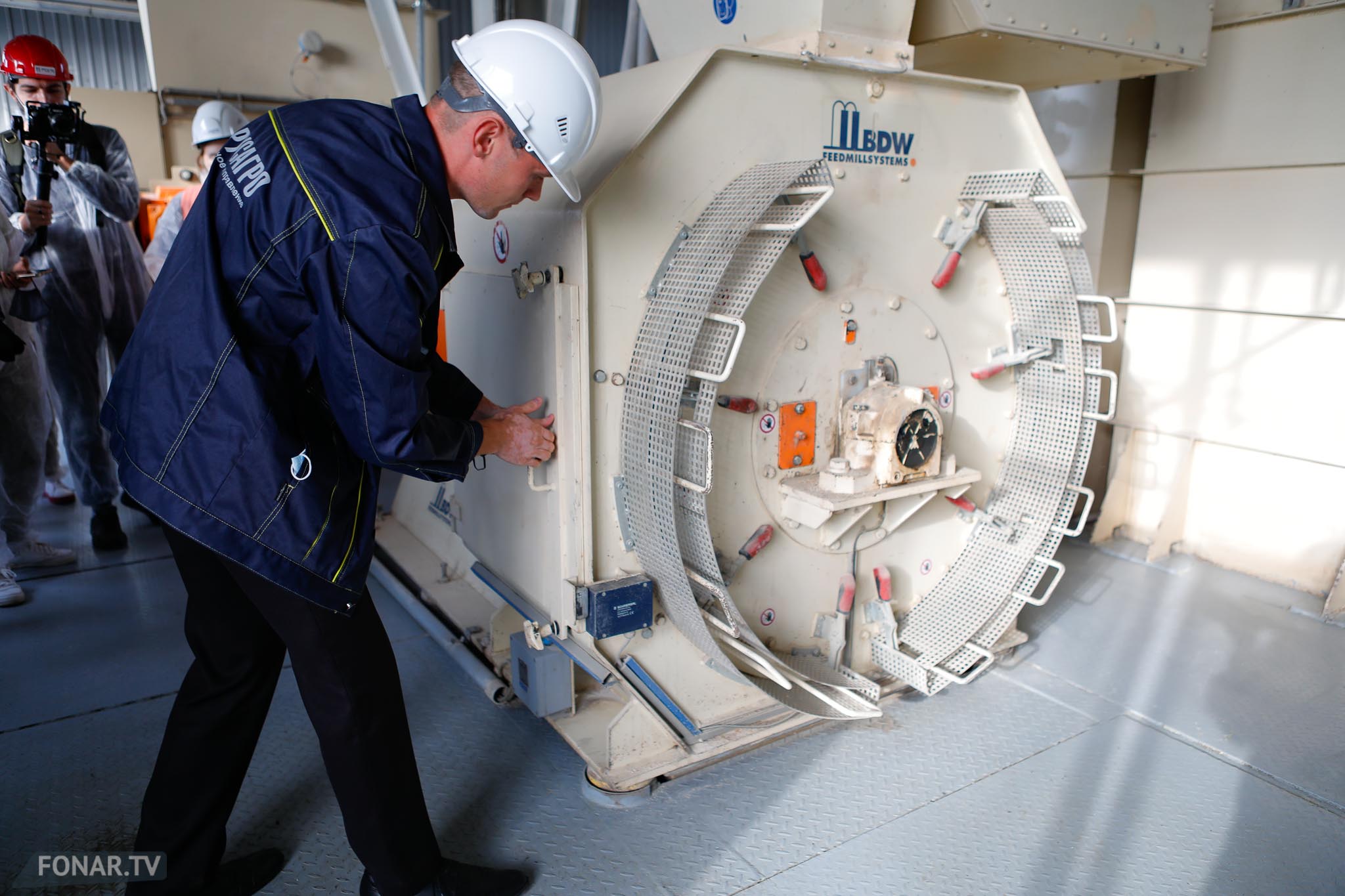
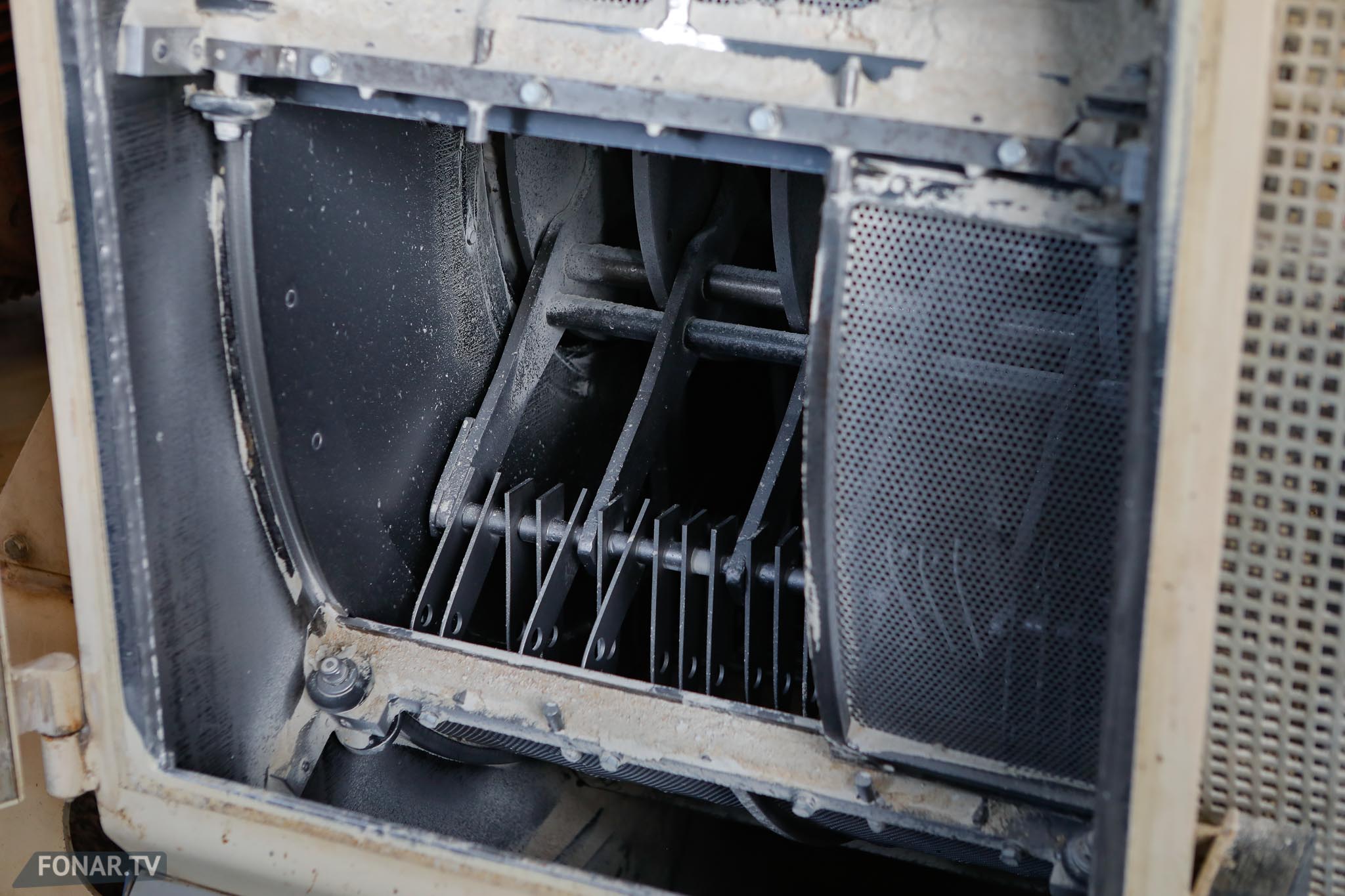
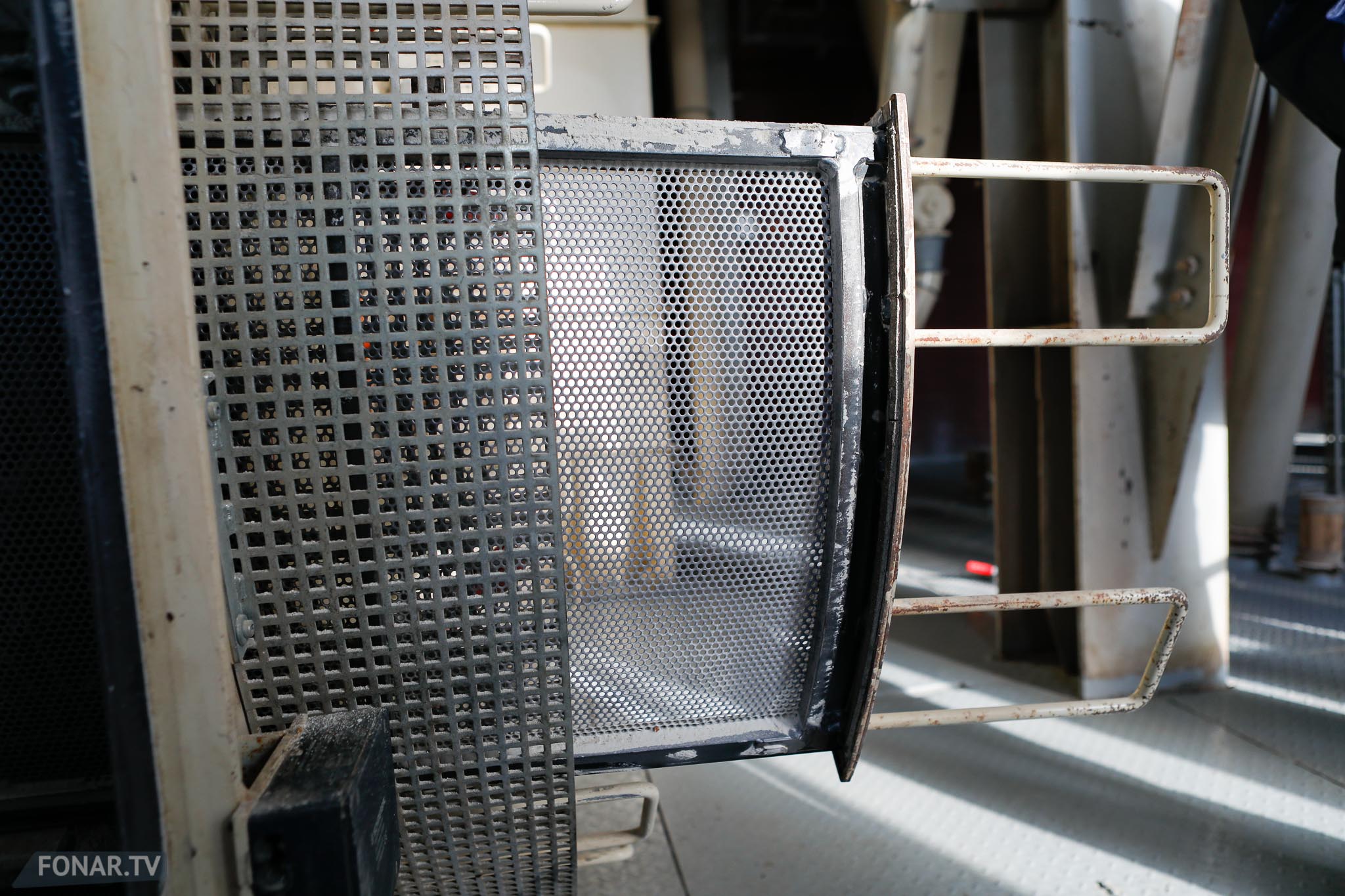
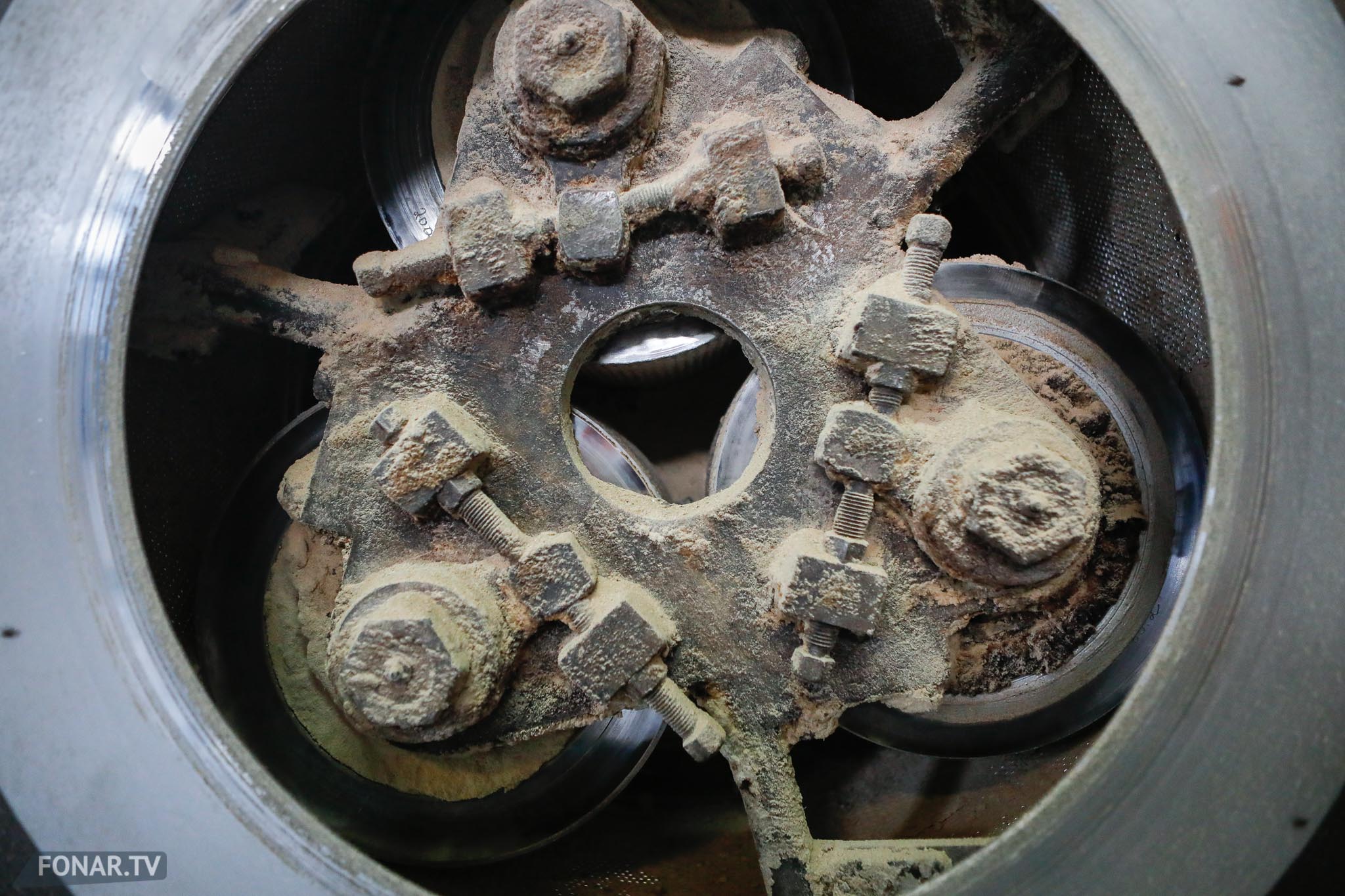
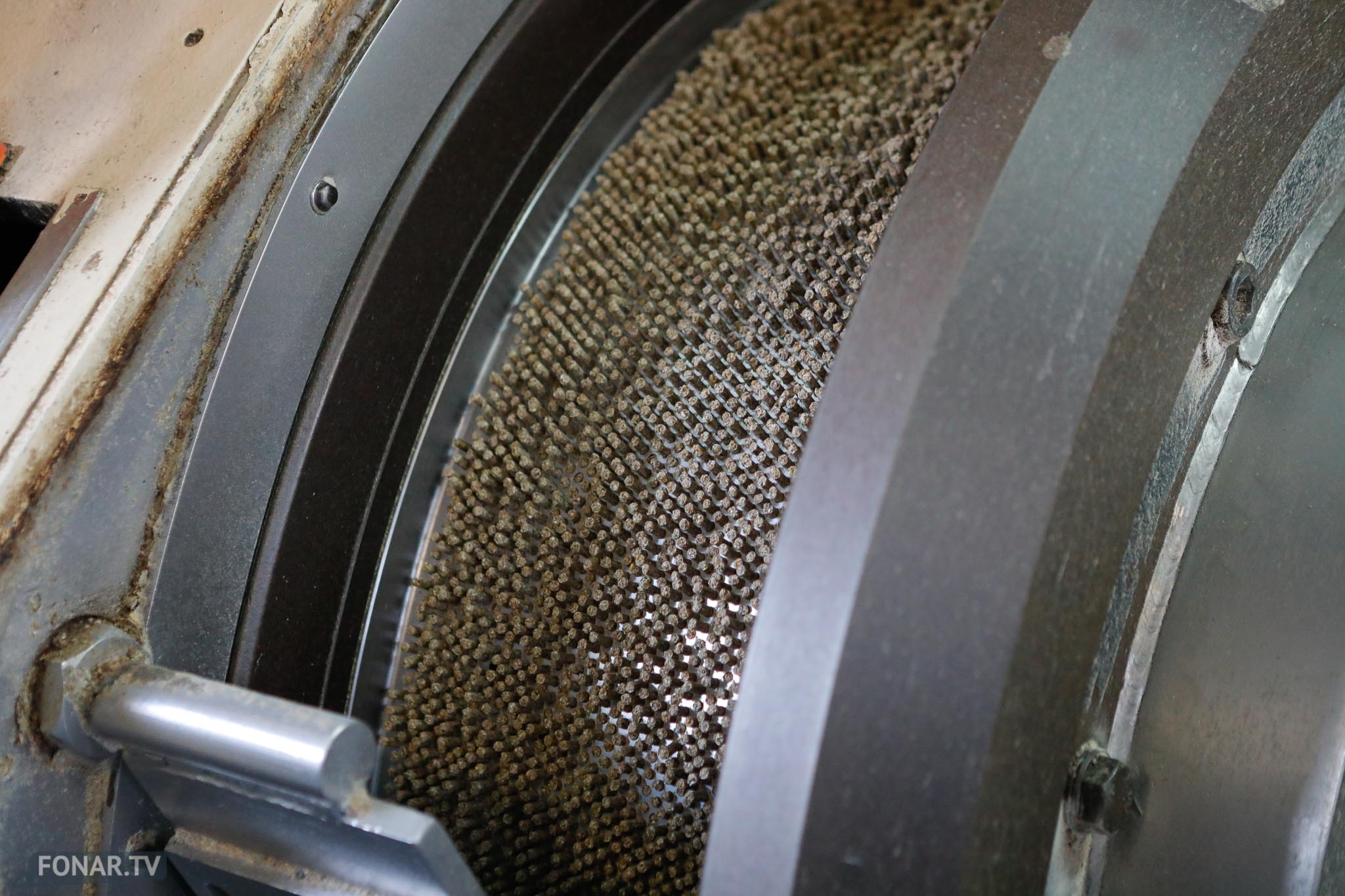
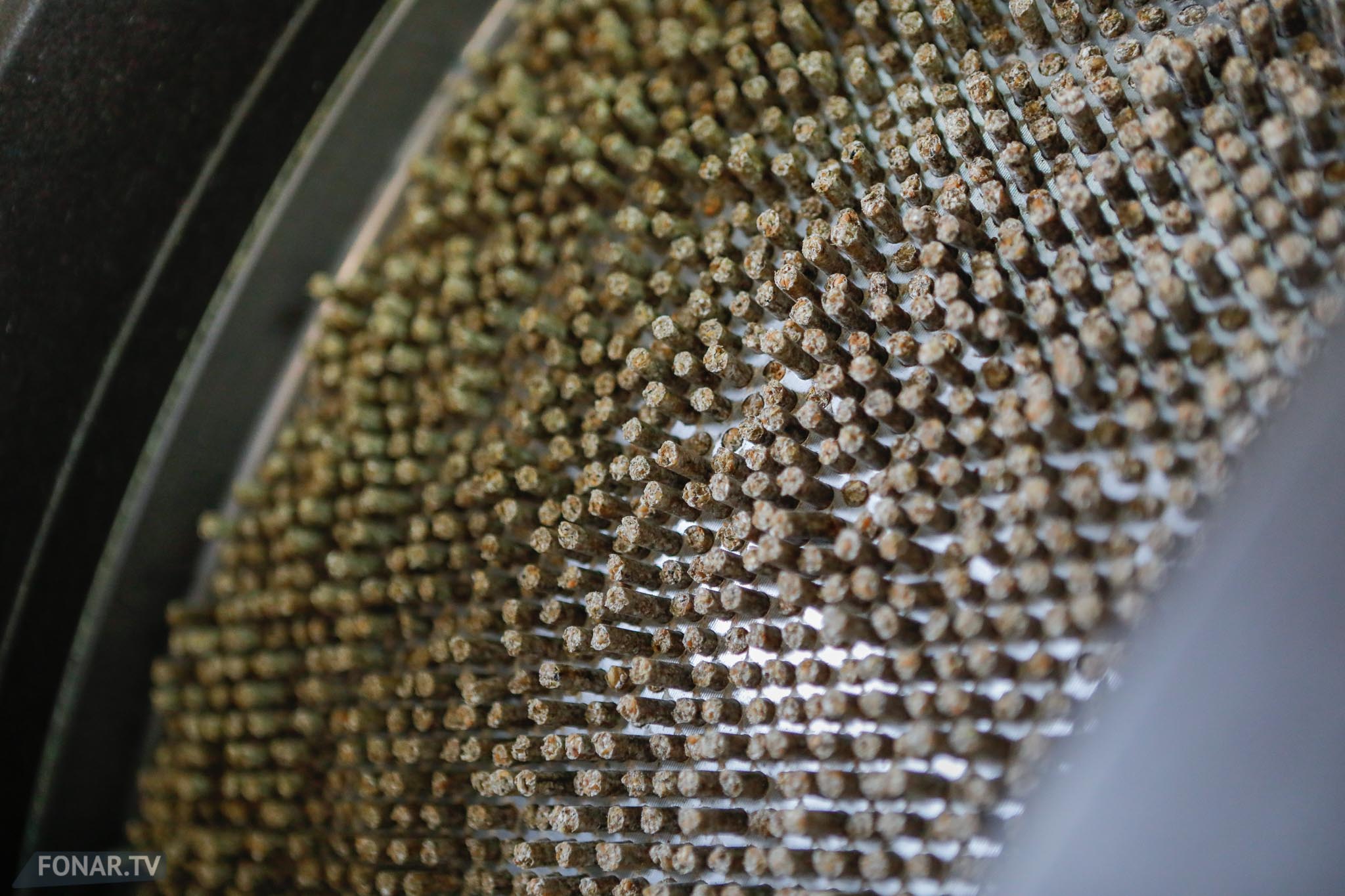
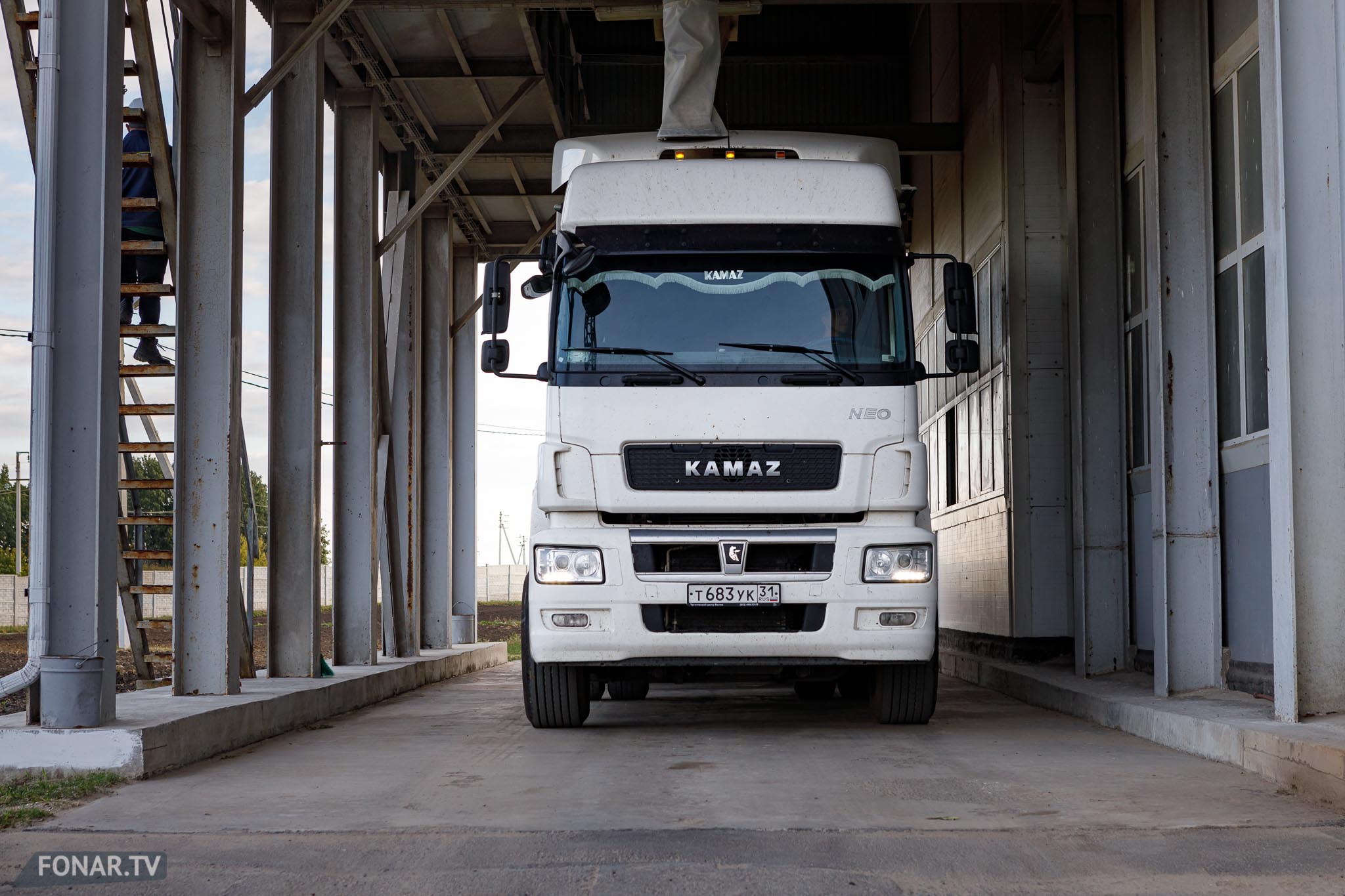
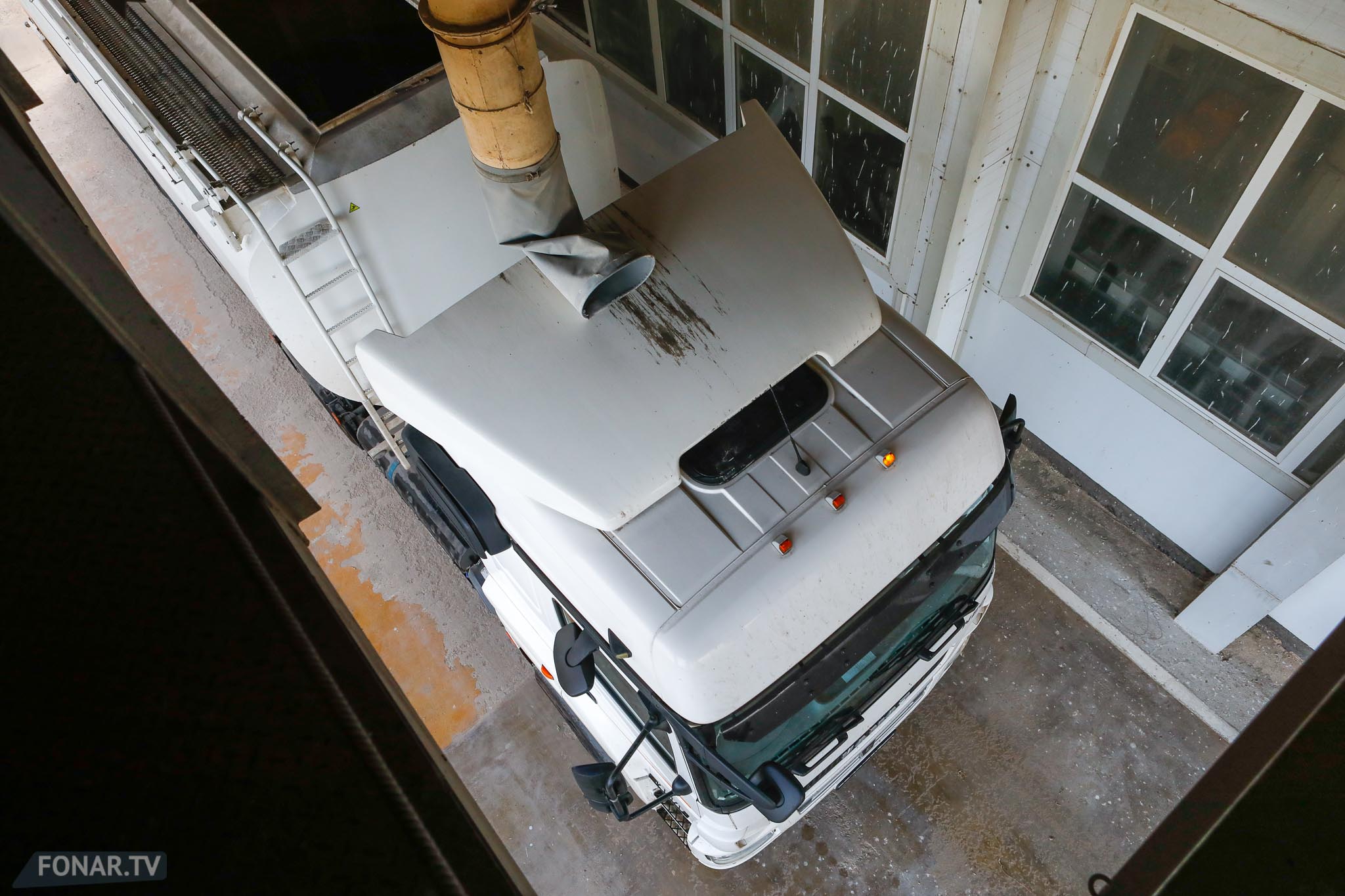
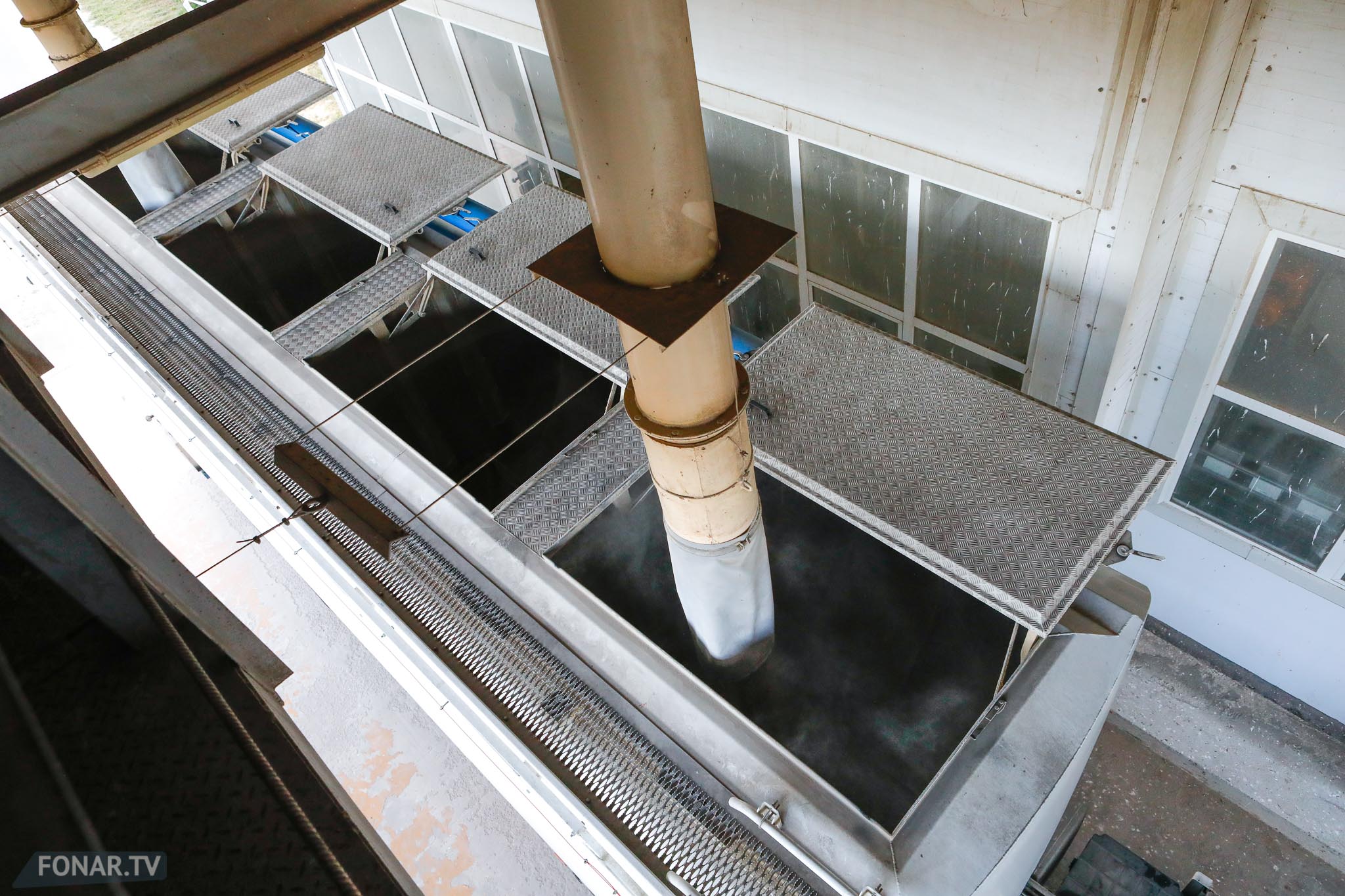
— После того, как комбикорм смешался, он оказывается опять на первом этаже. Потом он поднимается опять наверх и поступает на этап гранулирования. Паром этот комбикорм нагревается до 75-80 градусов и выдерживается в течение 3-5 минут. При этой температуре он насыщается влагой и только после этого попадает в гранулятор. В грануляторе с помощью пресса корм выдавливается через матрицу — её толщина составляет семь сантиметров, а диаметр — пять миллиметров. Всего в матрице 14 тысяч отверстий, через которые тонна комбикорма пролетает за три минуты. Так как эти гранулы горячие и влажные, они падают вниз в охладитель. Продуваясь потоком воздуха, они охлаждаются. После охлаждения мы имеем остывший твёрдый комбикорм, — объясняет начальник производства Дмитрий Фомин.
После охлаждения гранулы комбикорма опять поднимаются наверх через горизонтальный транспортёр и отправляются в бункер готовой продукции. В ячейке одного бункера готовой продукции (всего их 12 — прим. Ф.) хранится 60 тонн комбикорма. Итого предприятие может хранить у себя всего 720 тонн готового корма.
Последний этап — отгрузка комбикорма. Этим занимаются кормовозы — специальные машины, в которые через три рукава ссыпаются гранулы комбикорма.
Сколько нужно человек, чтобы завод работал?
Весь комбикормовый завод в Ивнянском районе автоматизирован, но за работой техники тоже должен кто-то следить. Для этого на производстве есть операторская, где за состоянием всех объектов присматривают три человека. На мониторы выведена система управления комбикормовым заводом, которая позволяет контролировать весь процесс.
Журналистам показывают, что в этот момент происходит на производстве. Мы видим, как реагируют датчики элементов безопасности на автоматическое включение или выключение маршрутов.
Далее наблюдаем за тем, как сотрудники принимают ячмень. На мониторах можно увидеть весь маршрут: зерно через завальную яму перемещают на десятый силос.
Если что-то случится с транспортом или не сработает какой-нибудь датчик безопасности — процесс автоматически остановится, появится сообщение об ошибке. Оператор это увидит и предпримет меры, чтобы устранить неполадку. При правильной настройке и использовании система полностью защищает от возникновения каких-либо чрезвычайных ситуаций: управление всеми процессами на заводе происходит с этого пульта. Именно здесь запускают все маршруты, смешивают и гранулируют компоненты.
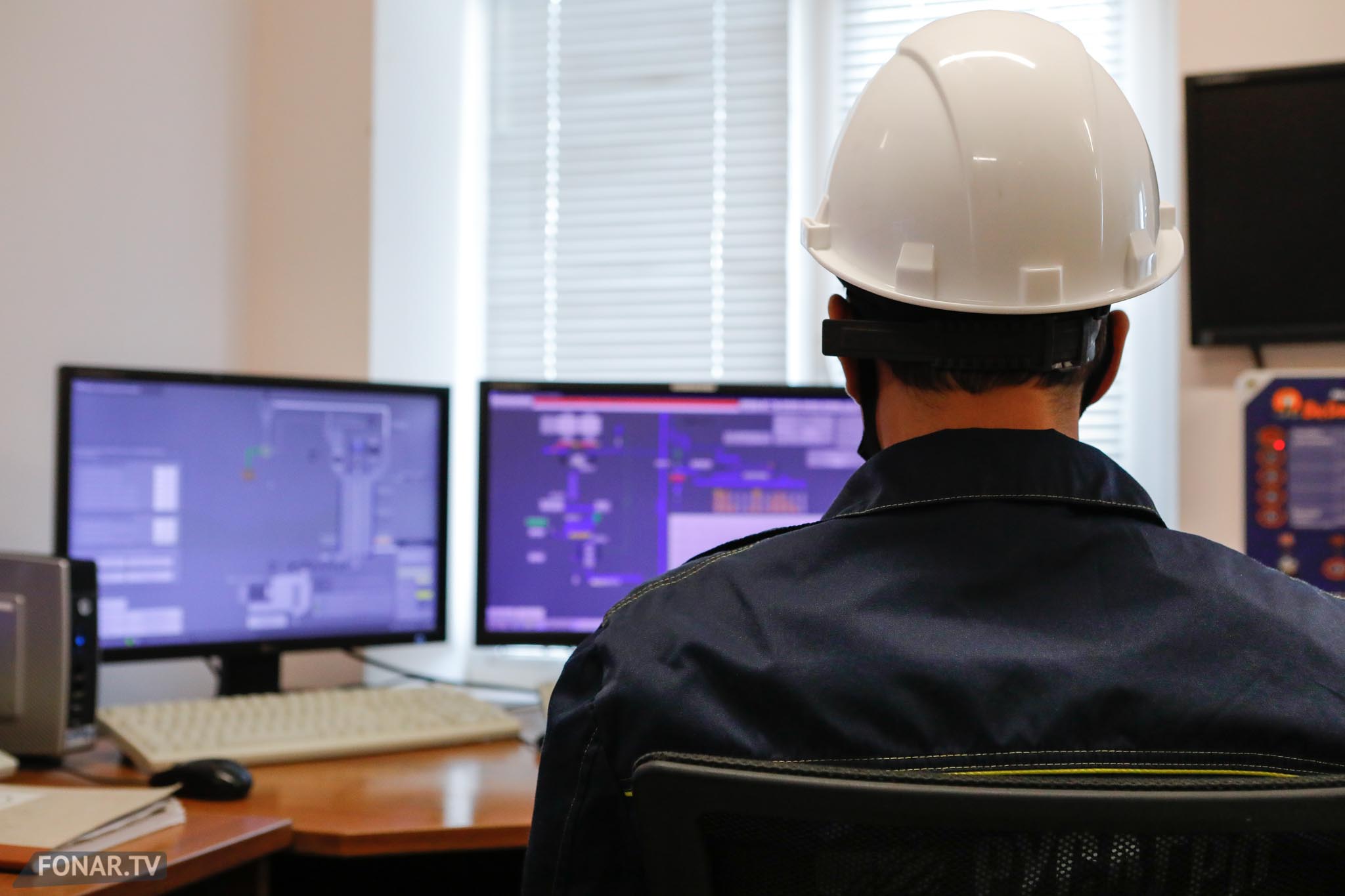
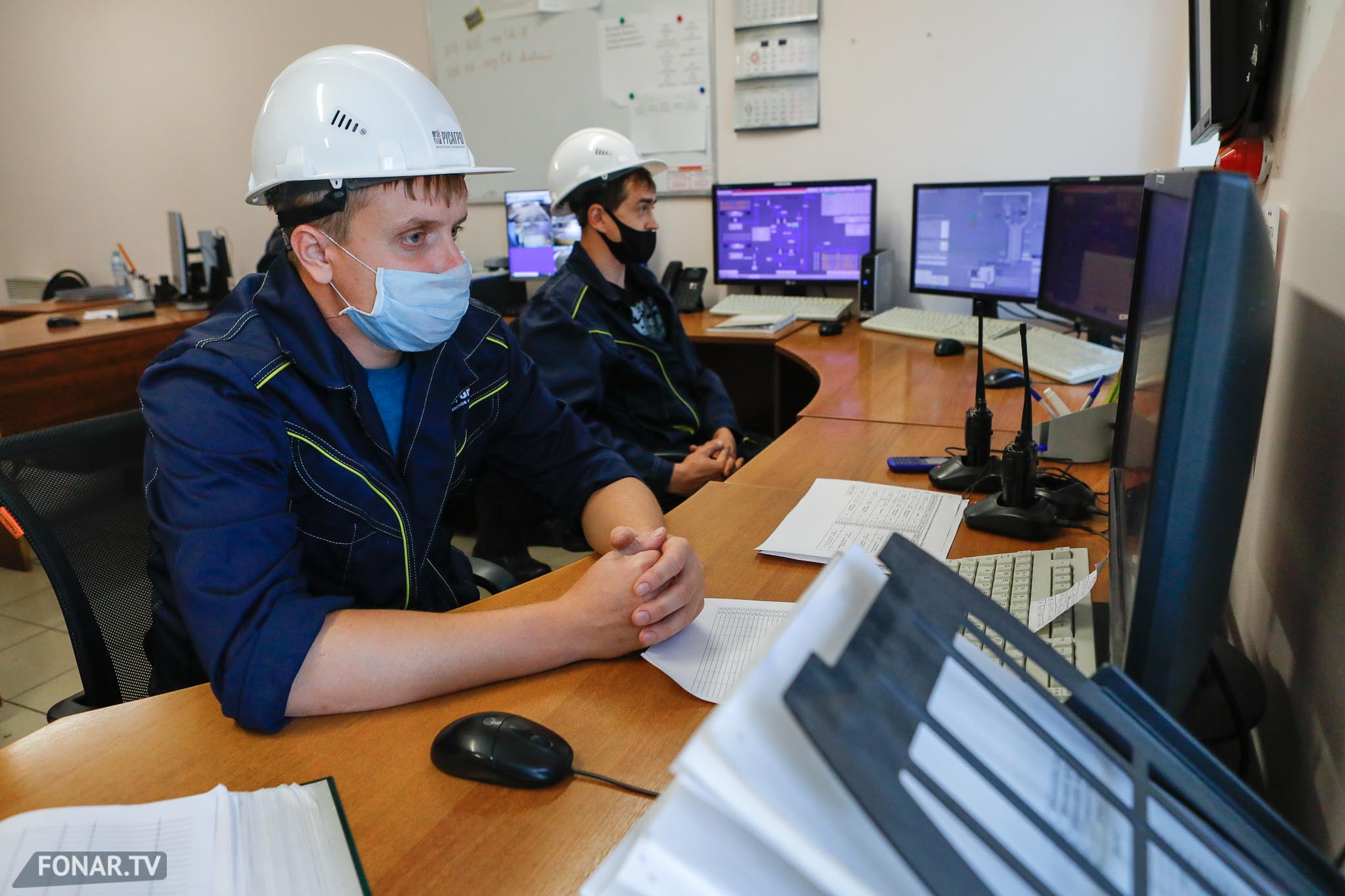
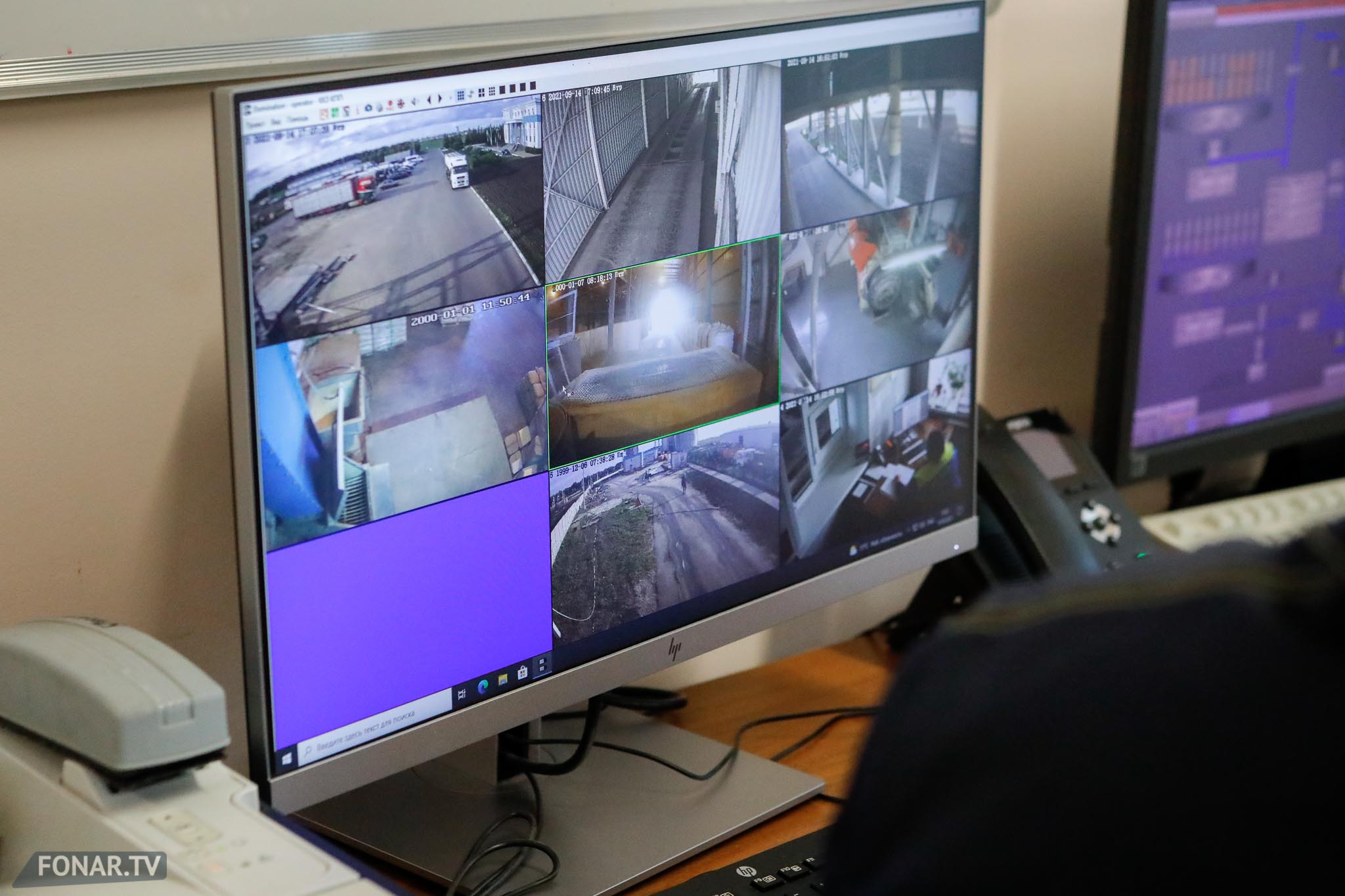
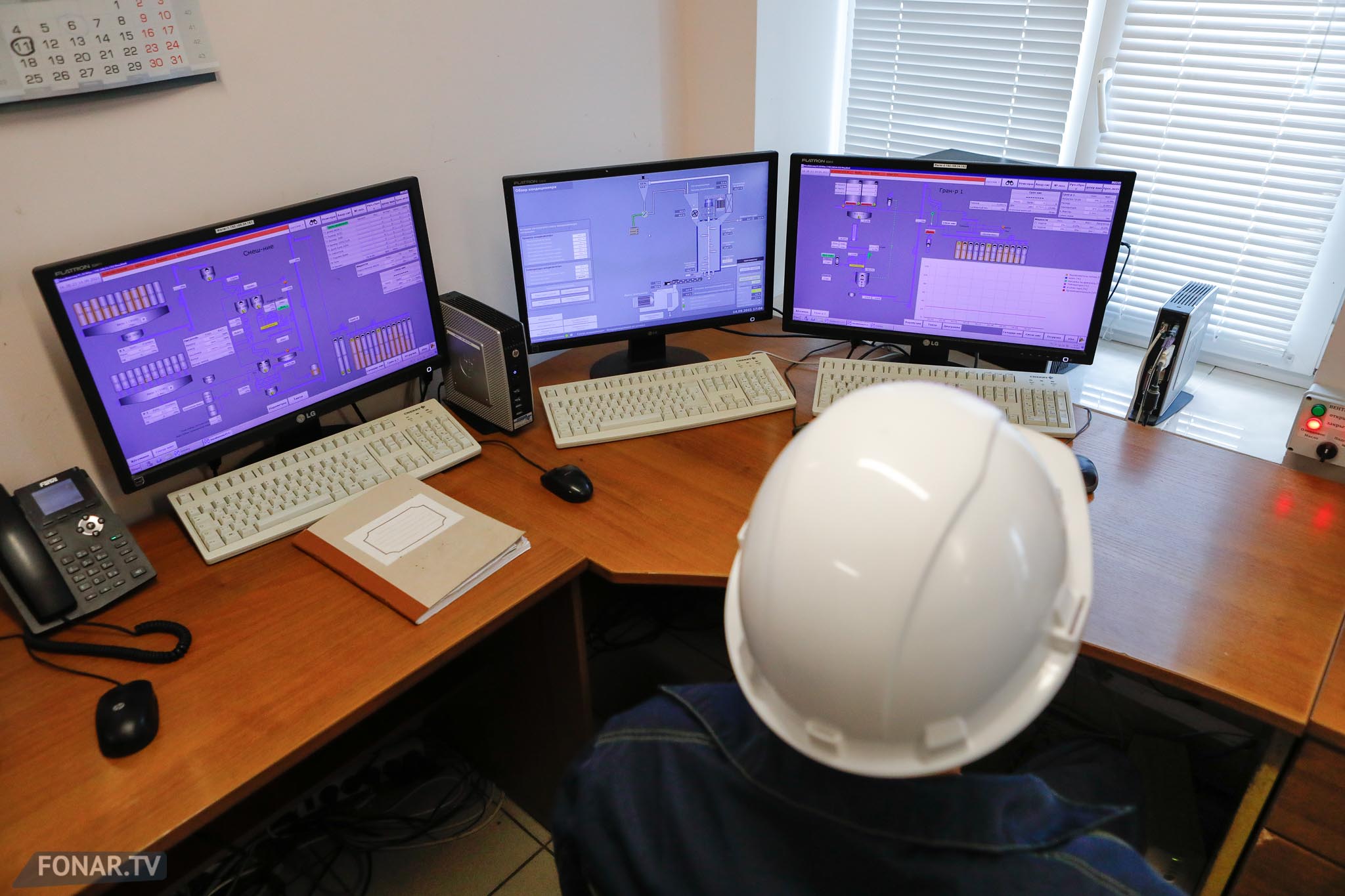
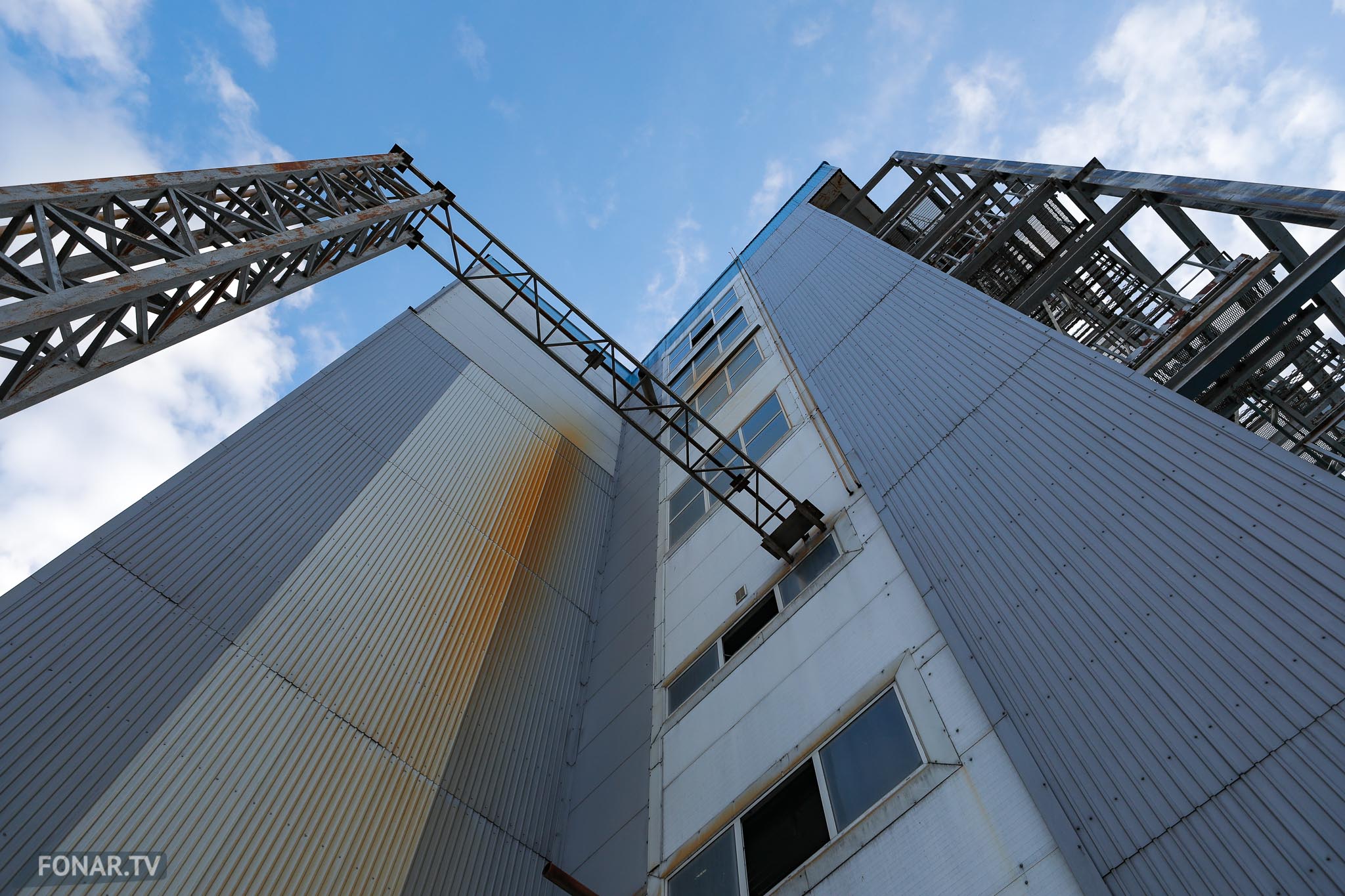
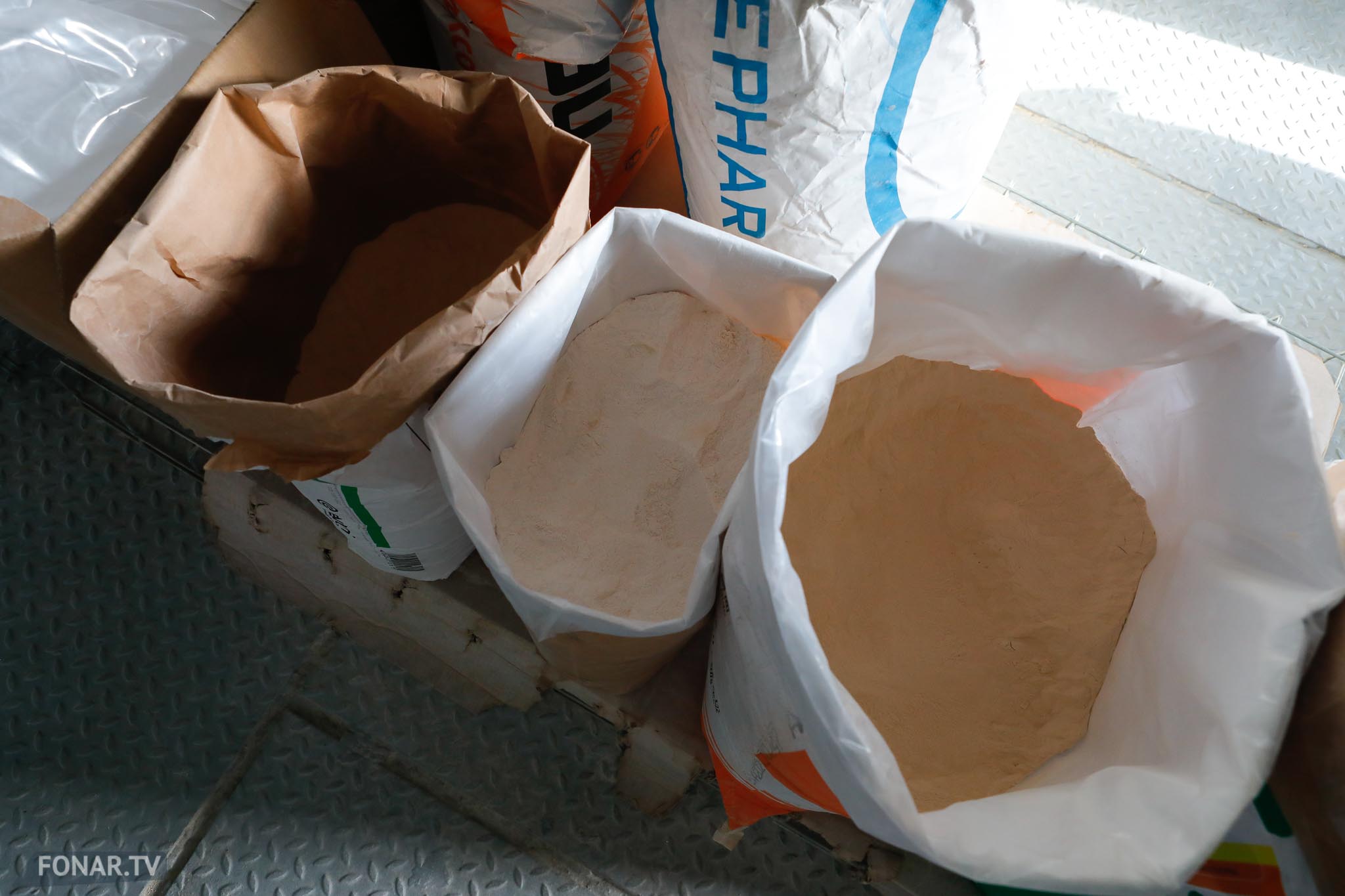
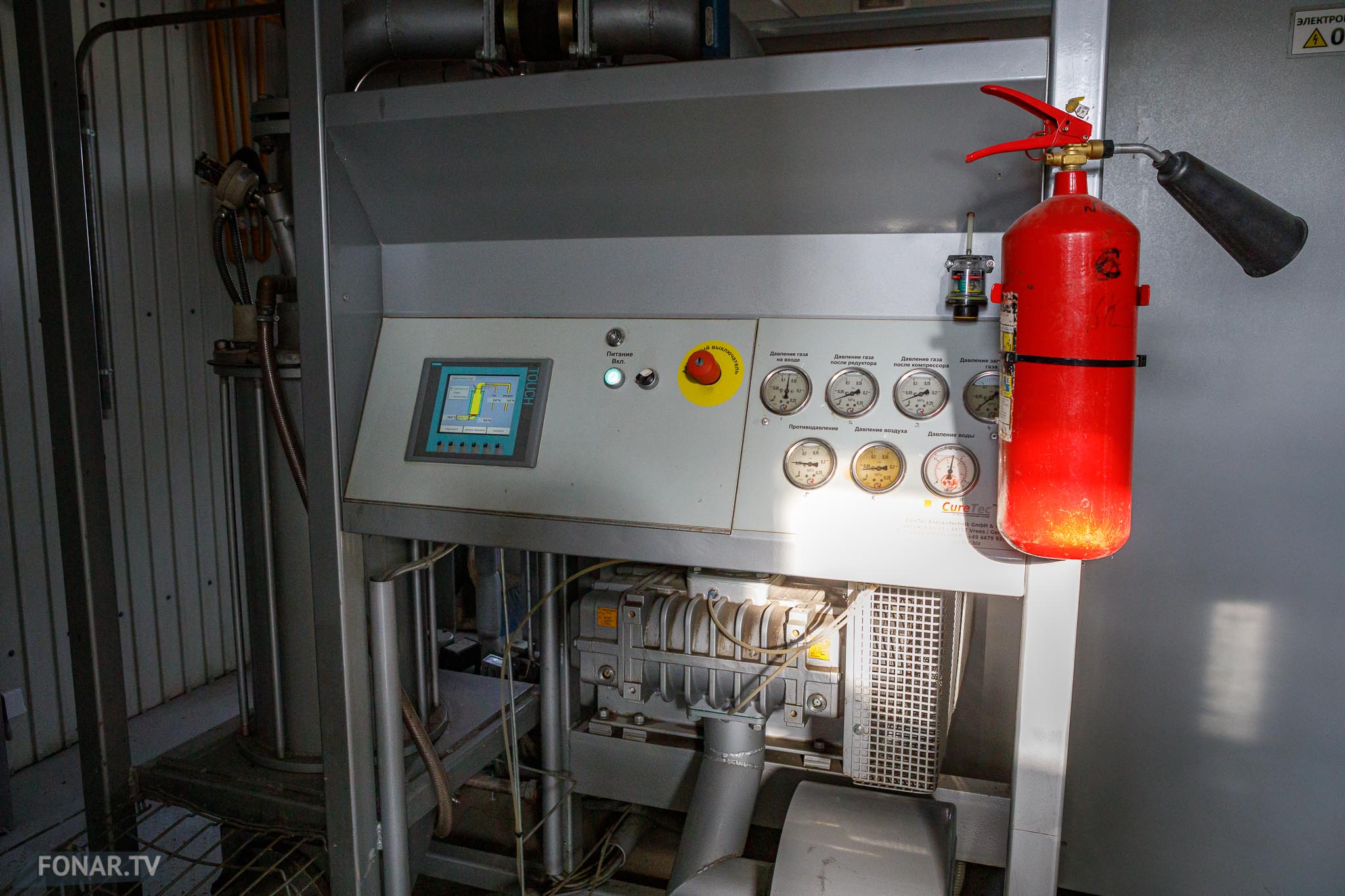
Помимо операторов на заводе работает ещё один человек, который вручную замешивает компоненты в соответствии с рецептом. Он трудится в берушах и респираторе, потому что вещества имеют специфический запах и раздражают слизистую носа. На рабочем мониторе у него отображается перечень компонентов, которые нужно насыпать, и их объём. Он их взвешивает и насыпает в специальный отдел, дальше — дело за техникой.
Небольшой объём веществ и других компонентов доставляют рабочему на лифте. Дорогостоящие вещества, вводимые в слишком малой дозировке по 100-200 граммов, добавляют с ручного пульта — аппаратчик наблюдает и взвешивает их с помощью лабораторных весов и тары, а потом вводит данные в ручной пульт. После этого нажимает подтверждающую кнопку, завершая дозирование на этот замес. Получившийся замес сбрасывают дальше на смешивание. Что происходит во время смешивания и дальше — вы уже знаете.
Что ждёт завод в будущем?
Так как компания «Русагро» увеличила количество производственных площадок и выработку продукции, увеличились и производственные мощности завода. Поэтому в планах руководства — реконструкция завода и увеличение его производительности с 15 до 20 тонн в час. Для этого хотят построить отдельную котельную, заменить оборудование, предназначенное для обработки паром, увеличить мощность гранулятора — всё это позволит вырабатывать корма с большей производительностью и закрыть все потребности компании.
— Корм, который производится, предназначен для животных компании. То есть, основная задача — закрыть внутренние площадки, но при необходимости мы сможем отгружать корма на сторону, если появится такая необходимость. Сейчас транспортировка кормов осуществляется в Белгородской области, но часть корма перемещается и в Тамбов по их заявкам. При увеличении спроса на корм у площадок животноводства мы часть корма сможем также поставлять и им, — добавляет Сергей Стронин.